Latest stories

Iran is gaining credibility across the Muslim world

Xi's big adventure to keep Europe open and onside
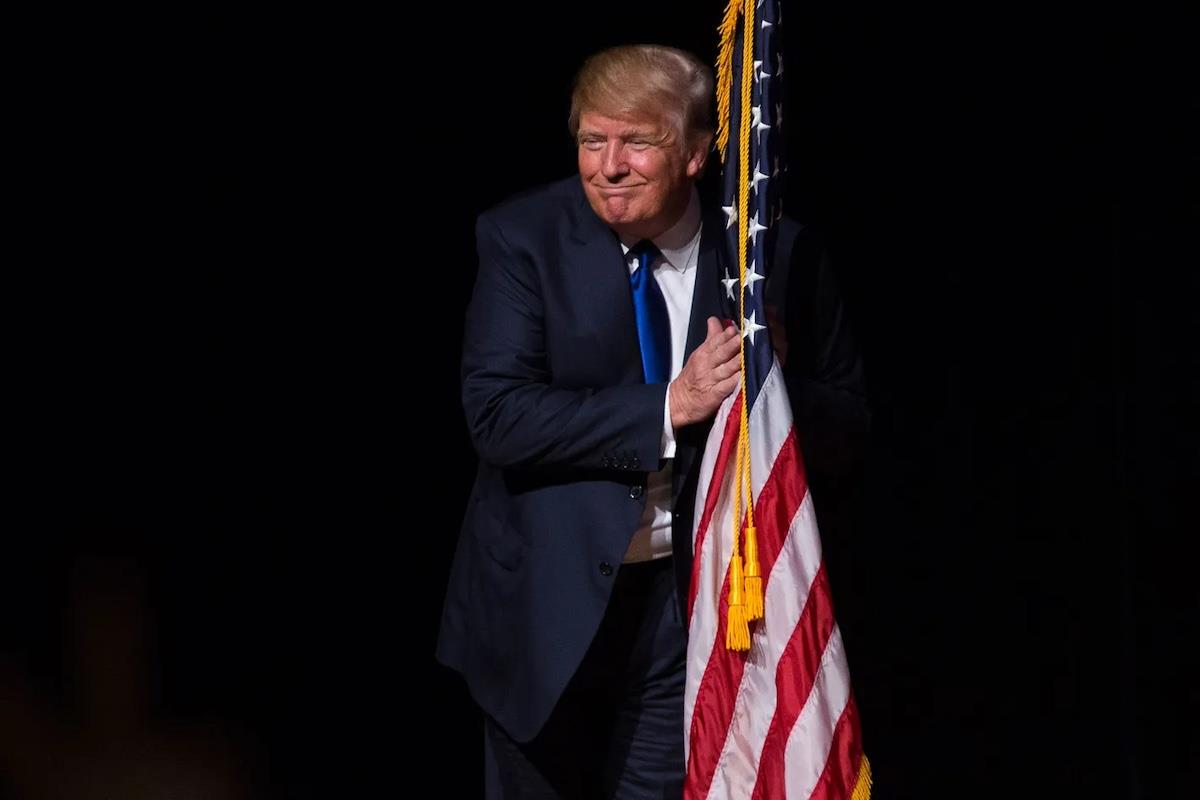
What Trump's 'America First' would mean for the world Five former employees from the US told
Rest of World
that TSMC engineers sometimes falsified or cherry-picked data for customers and managers. Sometimes, the engineers said, staff would manipulate data from testing tools or wafers to please managers who had seemingly impossible expectations.
Other times, one engineer said,“because the workers were spread so thin, anything they could do to get work off their plate they would do.”
Four American employees described TSMC culture as“save face”: Workers would strive to make a team, a department or the company look good at the expense of efficiency and employee wellbeing.
Pointless busy work just to please the boss? Hmm, I've heard that story before.
Kyle Chan, writer of the blog High Capacity, had
some interesting thoughts on the matter :
Which brings me to my next point.
Management or macroeconomics? TSMC is certainly one of the world's most successful companies - a true national champion, and a major victory for
industrial policy . But there are a number of reasons why its success relative to American chipmakers, as well as its struggles in the US market, might depend on economic factors outside the company and unrelated to Taiwanese culture.
First of all, much has been made of how TSMC took chip manufacturing market share from Intel, Samsung, and other companies that design and build their own chips in-house.
In addition to whatever Taiwanese cultural factors might be at play, this success is generally attributed to TSMC's“foundry” model - instead of making its own chips, it makes everyone else's chips, allowing it to specialize in the manufacturing process and cross-apply techniques and lessons from one type of product to another.
But you know who else can't make chips as well as TSMC?
Any other Taiwanese company in existence. If you look at a chart of revenue for chipmakers in Taiwan, it's just TSMC towering over all the rest:
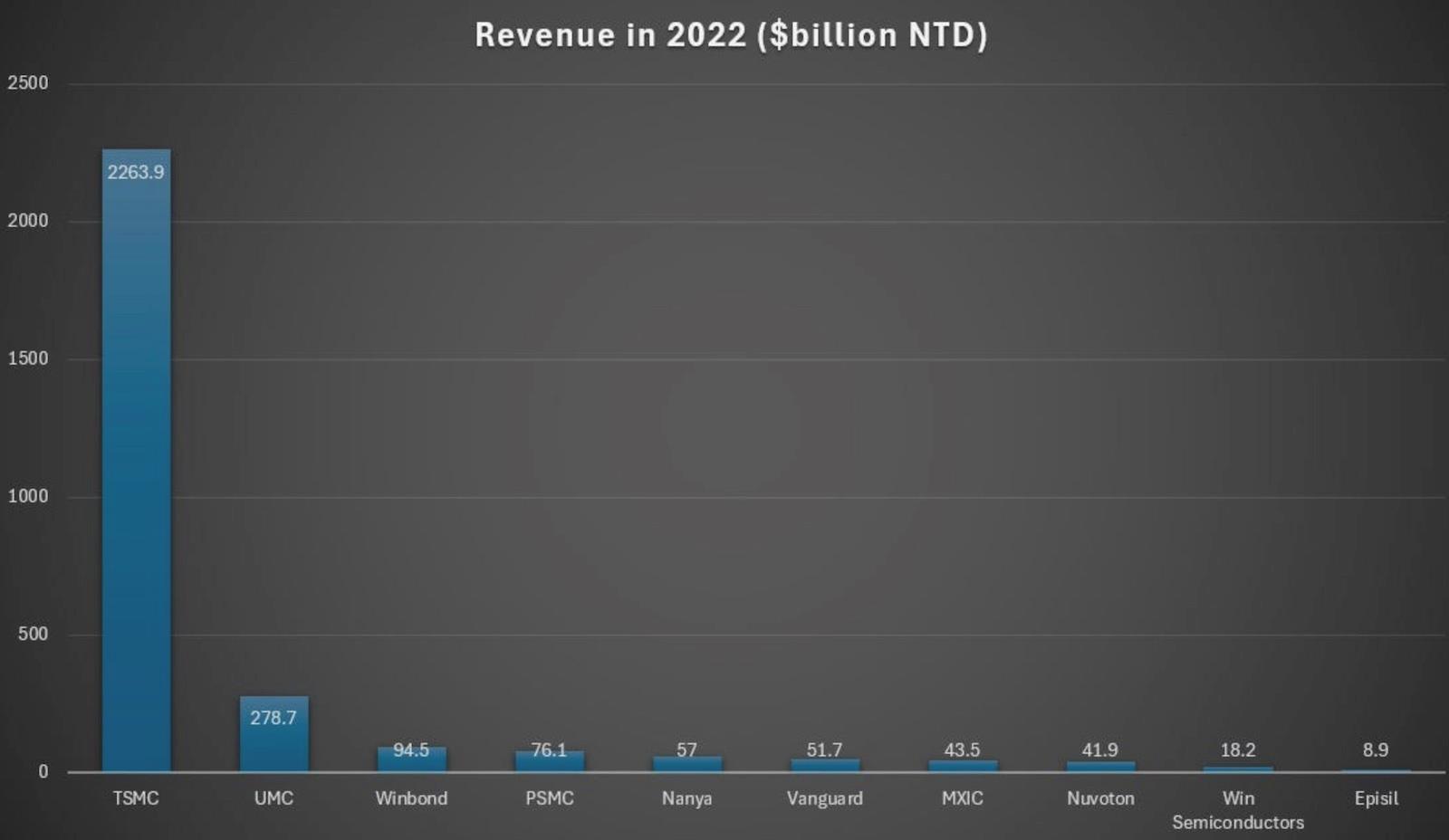
Source: Taiwan Semiconductor Industry AssociationAll together, TSMC's competitors have only 30% of its revenue. This is why no one is talking about building Winbond factories in Arizona, or discussing whether the US would go to war to protect Nuvoton from a Chinese invasion. Unlike Japanese auto companies in the 80s, or even Taiwanese PC makers in the 2010s, there is precisely
one
top chipmaker in Taiwan.
This is why TSMC pretty much gets its pick of Taiwanese talent, in terms of both skill and work ethic. Other companies don't get this benefit; if you're a top Taiwanese chip engineer, TSMC is just where you go work. So the engineers at TSMC aren't representative of Taiwanese skills and work ethic as a whole; they're a special, hyper-selected elite.
And what's more, TSMC doesn't have to pay very much for these top performers. In 2021,
the median salary at TSMC was US$64,874
in US dollars, with a bonus of
about $40 ,000 for a total of about $105,000.
In the tech world, that's nothing. That's less than an entry-level American software engineer makes right out of college
working for Visa , the credit card company.
Why does TSMC get top workers for such low pay? Well, one big reason is that Taiwanese workers just don't make very much in general. The average salary for full-time employees in Taiwan
is $22,242 . That's less than a minimum-wage worker
makes in Missouri or South Dakota . So in Taiwan, a TSMC salary is fairly big bucks.
Why are wages so low in Taiwan? One reason is that Taiwan is poorer than the United States. Another reason is that Taiwan makes sure to
keep its currency very cheap
relative to the US dollar, probably in order to improve the competitive position of companies like TSMC.
Meanwhile, TSMC's Arizona fabs have to compete for talent against other American tech companies. A typical hardware engineer at Apple gets paid somewhere around
$200,000 to $300,000 ; chip companies tend to pay a bit less, but still more than what TSMC workers get in Taiwan. But it's not just the hardware industry TSMC has to compete with in America; it's the
software
industry too.
A smart young American can choose to learn how to build chips or how to write code; the talent required is not very different. And if they choose to write code, they will generally get paid more. A typical software engineer at Google will get paid around $300k-$400k; for Facebook
it's more like $300k-$500k . (Meanwhile, try naming a Taiwanese software company.)
And make no mistake: Top American performers often work very, very hard. High earners in America
work hard in general , and many top people are putting in those 70-hour workweeks. Many young lawyers and doctors do this, as do employees at some tech companies
like Tesla , and many company founders and startup employees.
In its heyday under Andy Grove, Intel had
an intense, punishing work culture
not unlike TSMC. But they have to have some special motivation in order to do this - either the promise of a very high salary, or the promise of a big exit for their startup, or at least the pride of working as a doctor or for a prestigious company like Tesla. TSMC gets a lot of headlines, but it's not prestigious in America the way it is in Taiwan.
Even Taiwanese workers in the U.S. are tempted by the lure of better jobs elsewhere, as Zhou's article notes:
That's what TSMC is really competing with at its Arizona fabs. It's having to pay a multiple of what it would pay in Taiwan, for workers who are less elite and less passionately committed to the company.
This is not an advantage of Taiwanese management or Taiwanese culture - it's a function of the fact that Taiwan is a less wealthy country than America, and one that has chosen to throw many of its best people into a single national champion company. Compared to that, of course making chips in Arizona is going to be more expensive.
Americans can learn East Asian manufacturing methods just fine So far, I've argued that:
East Asian management culture is not necessarily the best, even if it looks very intense and hard-working, and
TSMC's cost disadvantages in Arizona depend on macro factors, not just on cultural differences (or perhaps not on cultural differences at all).
But it's also the case that sometimes, East Asian companies come up with important management innovations that really do raise productivity a lot. But when they do,
American workers can learn and apply those innovations
in America.
The prime example here is the Japanese car industry. In the 1980s, Japanese carmakers started exporting a lot fewer cars from Japan to the US, and started making a lot more cars in the US:

Source:
JAMA Every Japanese carmaker has
huge auto plants in the U S, and many of
the most American-made cars
are built by workers working for Japanese brands.
This was an absolutely massive experiment in foreign direct investment by an East Asian country into the US. At the time, Japanese auto manufacturing productivity was much higher than American productivity, so the Japanese companies had much to teach their American workers.
And teach them they did. American car plants adopted practices such as the kanban scheduling system, the kaizen system of continuous improvement (originally conceived of in the US but put into practice in Japan), and many others.
These practices mostly came from the famous Toyota Production System, but they form the basis of what we now know as
lean manufacturing . Japanese car companies implemented these techniques at their factories in America but they've diffused widely since then - not just to American car companies, but to many other industries throughout corporate America.
American factories were successfully able to learn these Japanese management techniques.
Detailed comparisons
between vehicles built in Japan and those built in the US show only very small differences.
And the cars that Japanese brands build in America are internationally competitive, even in spite of America's uncompetitive exchange rate. Consumers in Korea are
buying Nissan Altimas
made in Tennessee and
Honda Accords
made in Ohio. Australians are
buying Toyota Highlanders
made in Indiana.
If American workers can learn how to build cars like Japan, it seems like a good bet that they can learn to build chips like Taiwan. But Japanese carmakers started trying to teach American workers their tricks in the late 1980s; TSMC has barely started trying. Viola Zhou's article indicates that TSMC isn't even to the stage of being able to
talk
to American workers:
Language barriers are the very earliest thing that companies have to overcome when they build factories overseas. The fact that TSMC still can't even communicate in English means that it's still very early days.
That's why it's so unhelpful to declare that TSMC's factories in America are a“debacle” just because of a modest delay at the outset. Foreign direct investment is a long, winding, arduous journey. It's not the kind of thing where we should expect everything to run perfectly smoothly on the first try.
Meanwhile, the mystique of East Asian culture is just not a good lens through which to view challenges like this one. Cross-country cultural differences are real but they aren't as impactful on business as people like to think. Humans are humans, and they can learn.
This
article
was first published on Noah Smith's Noahpinion
Substack and is republished with kind permission. Read the
original and become a Noahopinion
subscriber
here.
Already have an account?Sign in Sign up here to comment on Asia Times stories OR Thank you for registering!
An account was already registered with this email. Please check your inbox for an authentication link.
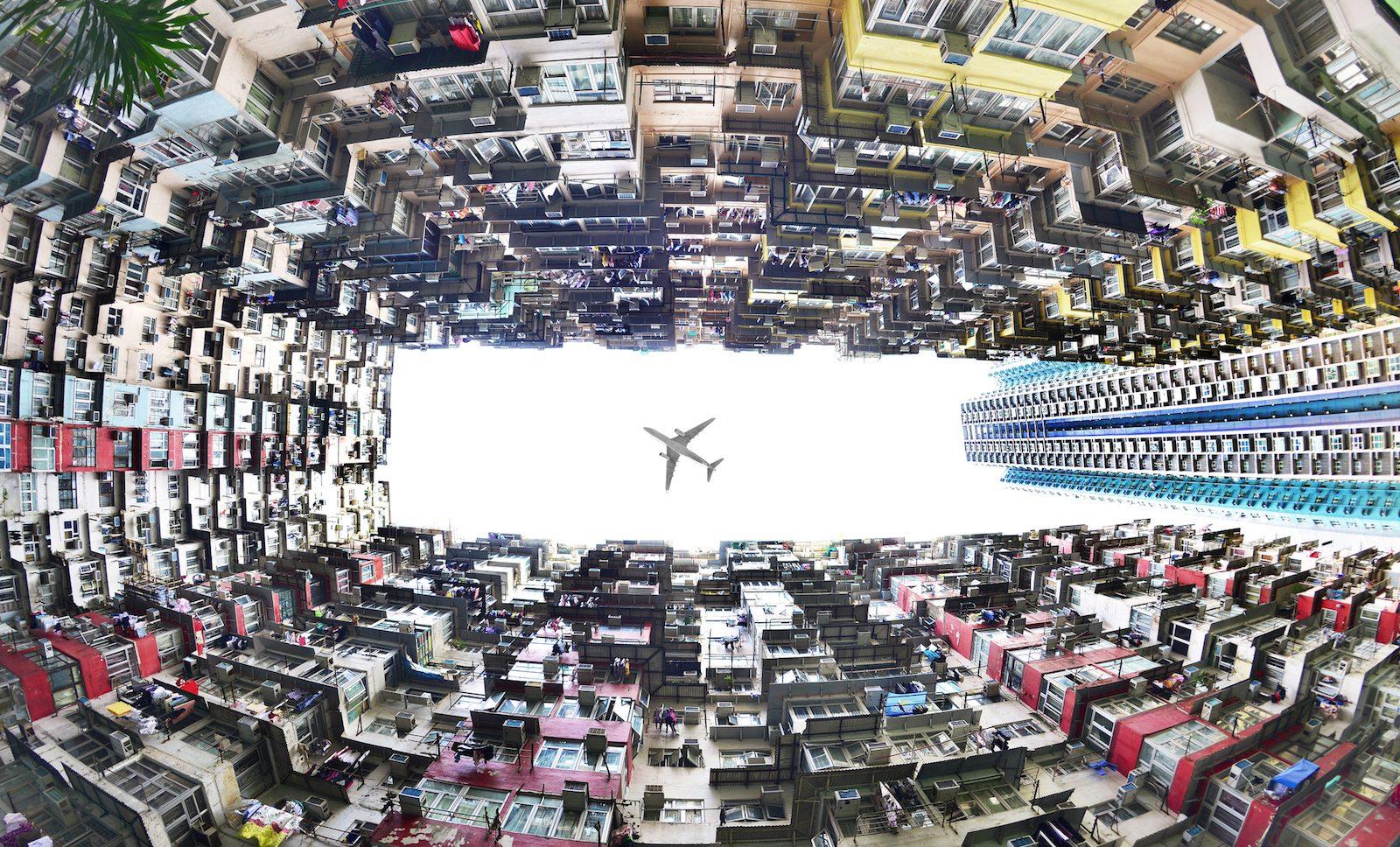
Sign up for one of our free newsletters The Daily ReportStart your day right with Asia Times' top stories AT Weekly ReportA weekly roundup of Asia Times' most-read stories