ZERO BRINE's Site II pilot launches in Rotterdam Port
(MENAFN- Editorial) ROTTERDAM, 21 AUGUST 2020 — At the Port of Rotterdam, one of the largest petrochemical clusters in Europe, the ZERO BRINE project has launched its second site as part of the demonstration of industrial circularity combining residual heat and wastewater streams to eliminate brine effluent (zero brine discharge) in the production of demineralised water.
Demineralised water is an essential commodity required for the many industrial processing facilities in the Rotterdam Port. This water is provided by the Evides Demineralised Water Plant (DWP) – one of the largest demineralised water production facilities in Europe
Site II pilot at Plant One Rotterdam. Photo: ZERO BRINE
While the Site I pilot treated the spent regenerant solution of the IEX unit to recover high purity calcium, magnesium, salt, and clean water, Site II will aim to use an innovative design to treat the reverse osmosis (RO) concentrate of the DWP using a combination of new and existing technologies to recover sulphate salts, sodium bicarbonate, regeneration solution (NaCl rich stream), and clean water.
ZERO BRINE''s Executive Project Coordinator, Roelof Moll, commended the partners contributing their technologies for the Site II operations. "International cooperation works as key to success in technology development for a circular economy," he stated.
The Pilot Site II technologies are provided by project consortium members including UK-headquartered water treatment company Arvia (TOC removal), Dutch water treatment company Lenntech (nanofiltration and RO), the Delft University of Technology (Eutectic Freeze Crystallizer), and the National Technical University of Athens (evaporator). The pilot is also coordinated by the Delft University of Technology in the context of the ZERO BRINE project.
The ZERO BRINE project is facilitating the implementation of the EU Circular Economy package and the Sustainable Process Industry through Resource and Energy Efficiency (SPIRE) Roadmap in various process industries by developing the necessary concepts, technological solutions and business models to redesign the value and supply chains of minerals and water while dealing with present organic compounds in a way that allows their subsequent recovery. The project sets a precedent for industrial circularity and a new generation of innovative, resource-efficient European business.
Two additional pilot plants have yielded promising results at a coal plant in Gliwice, Poland and a silica plant in Zaragoza, Spain, while a textile factory pilot installation near Istanbul in Turkey is currently under construction.
Demineralised water is an essential commodity required for the many industrial processing facilities in the Rotterdam Port. This water is provided by the Evides Demineralised Water Plant (DWP) – one of the largest demineralised water production facilities in Europe
Site II pilot at Plant One Rotterdam. Photo: ZERO BRINE
While the Site I pilot treated the spent regenerant solution of the IEX unit to recover high purity calcium, magnesium, salt, and clean water, Site II will aim to use an innovative design to treat the reverse osmosis (RO) concentrate of the DWP using a combination of new and existing technologies to recover sulphate salts, sodium bicarbonate, regeneration solution (NaCl rich stream), and clean water.
ZERO BRINE''s Executive Project Coordinator, Roelof Moll, commended the partners contributing their technologies for the Site II operations. "International cooperation works as key to success in technology development for a circular economy," he stated.
The Pilot Site II technologies are provided by project consortium members including UK-headquartered water treatment company Arvia (TOC removal), Dutch water treatment company Lenntech (nanofiltration and RO), the Delft University of Technology (Eutectic Freeze Crystallizer), and the National Technical University of Athens (evaporator). The pilot is also coordinated by the Delft University of Technology in the context of the ZERO BRINE project.
The ZERO BRINE project is facilitating the implementation of the EU Circular Economy package and the Sustainable Process Industry through Resource and Energy Efficiency (SPIRE) Roadmap in various process industries by developing the necessary concepts, technological solutions and business models to redesign the value and supply chains of minerals and water while dealing with present organic compounds in a way that allows their subsequent recovery. The project sets a precedent for industrial circularity and a new generation of innovative, resource-efficient European business.
Two additional pilot plants have yielded promising results at a coal plant in Gliwice, Poland and a silica plant in Zaragoza, Spain, while a textile factory pilot installation near Istanbul in Turkey is currently under construction.
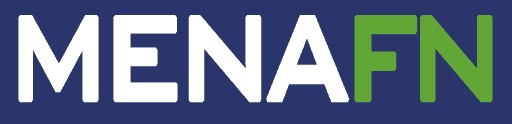
Legal Disclaimer:
MENAFN provides the
information “as is” without warranty of any kind. We do not accept
any responsibility or liability for the accuracy, content, images,
videos, licenses, completeness, legality, or reliability of the information
contained in this article. If you have any complaints or copyright
issues related to this article, kindly contact the provider above.
Most popular stories
Market Research

- Japan Ultrasound Devices Market Size Worth USD 887.0 Million By 2033 CAGR Of 5.4%
- Ecosync & Carboncore Launch Full Stages Refi Infrastructure Linking Carbon Credits With Web3
- Latin America Mobile Payment Market To Hit USD 1,688.0 Billion By 2033
- United States Lubricants Market Growth Opportunities & Share Dynamics 20252033
- Japan Smart Cities Market Size Is Expected To Reach USD 286.6 Billion By 2033 CAGR: 14.6%
- Blackrock Becomes The Second-Largest Shareholder Of Freedom Holding Corp.
Comments
No comment