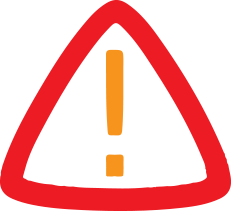
Comau Provides Geely With 'Powerful' Multi-Robot Solution
January 24, 2025 by Mark Allinson
Industrial automation specialist Comau has provided Geely, one of China's largest automotive brands, with a 'powerful process solution' using multiple robots to install motor rotors
The rapid market evolution of new energy vehicles (NEV) is revolutionizing electric drive systems, propelling motor assemblies toward unprecedented levels of integration, higher voltage capabilities, and enhanced power outputs.
As the driver of energy conversion, the electric motor plays a pivotal role in determining a vehicle's efficiency, reliability, and overall performance.
At the heart of every motor are the stator and rotor, two critical components that define its operational excellence.
Because the rotor is an intricate assembly of windings, magnet steel sheets, bearings, cores, and end caps, its production necessitates cutting-edge design methodologies and manufacturing techniques to ensure high-speed operation, extended durability, and optimal vehicle performance.
Indeed, the shift to advanced NEV motor technologies has significantly heightened the demands of rotor manufacturing, requiring increased precision, flexibility, and adaptability to varied product specifications.
This evolution presents a series of challenges, including component alignment, strict quality requirements, and the necessity for efficient, scalable production processes.
Traditional methods often fall short in addressing these complexities, leaving manufacturers in search of innovative solutions.
Comau's automated rotor assembly solutions are specifically engineered to tackle these challenges head-on.
With modular workstation designs and adaptable configurations, its systems deliver remarkable precision and efficiency while enabling seamless transitions between diverse product variants.
This, in turn, enables NEV manufacturers to excel in the dynamic and competitive marketplace by leveraging long-term scalability and operational agility.
Comau's rotor assembly lines incorporate advanced automation technologies to achieve efficient, high-performance production while setting new standards for flexibility and compatibility.
The integration of 3D vision technology, which is seamlessly incorporated into rotor core and shaft loading stations, ensures precise detection. It also facilitates the smooth adaptation to varying product specifications and thus enhances overall production accuracy.
To reduce downtime and maximize productivity, the optimized design incorporates lean manufacturing principles through space-efficient layouts and maintenance-friendly features, reducing downtime and maximizing productivity.
In fact, the system has been proven to achieve a First Time Through (FFT) rate exceeding 99 percent, with standard cycle times reduced to under 90 seconds.
When the Geely Group needed to ramp-up production of its high-quality electric drive components, Comau was tasked with developing and deploying a new e-drive assembly line that would guarantee high-speed, end-to-end production of the electric motor, gearbox and inverter at its Geely Vremt plant.
Comau provided Geely with a powerful process solution using multiple robots to install the motor rotors.
The automated line also features 3D vision positioning and guidance, automatic high-speed magnet installation, automatic injection of rotor cores and the automatic dual-position dynamic balance correction, magnetization – all of which contributes to ensuring higher quality and better throughput in less time.
Comau's innovative electrification solutions are further strengthened by decades of expertise and successful delivery of turnkey rotor production lines.
For example, the automated magnet insertion solution integrates vision systems and pressure monitoring to prevent misalignment or missing magnets. Real-time depth detection ensures precise positioning during the insertion process, meeting stringent quality standards.
Additionally, a multi-gripper design supports simultaneous pick-and-place operations, reducing the cycle time per magnet to under three seconds while maintaining extremely high accuracy.
Furthermore, to accommodate diverse product requirements, Comau provides multiple rotor fixation methods, including adhesive dispensing, plastic injection, and potting.
Its custom-designed dispensing nozzles surpass conventional designs by ensuring precise adhesive application, even in narrow magnet slots.
This approach guarantees uniform sidewall coverage while preventing overflow, enhancing rotor durability and performance under high-speed operating conditions.
The production lines also feature industry-leading automatic balancing technologies, utilizing high-precision components for weight addition and removal calibration. This ensures seamless adaptability across various products while maintaining equipment accuracy.
Another benefit of the solution is its full compliance with stringent NVH (Noise, Vibration, and Harshness) standards, which can contribute to improved bearing longevity.
Finally, the core shaft assembly process integrates advanced methods, combining liquid nitrogen cooling with rotor core heating to minimize assembly resistance. A pressure feedback system ensures consistent quality and dependable performance for every unit produced.
These methods exemplify Comau's commitment to integrating cutting-edge technologies that enhance both product quality and operational efficiency.
Backed by over 50 years of manufacturing excellence and a proven track record in the NEV sector, Comau is successfully delivering tailored rotor assembly solutions to players of all sizes.
Not only do Comau's solutions meet the complex demands of modern manufacturing, but they also optimize production efficiency, reduce costs, and provide measurable business value.
All of which helps equipment manufacturers achieve a sustained competitive edge within the evolving NEV landscape.
Legal Disclaimer:
MENAFN provides the information “as is” without warranty of any kind. We do not accept any responsibility or liability for the accuracy, content, images, videos, licenses, completeness, legality, or reliability of the information contained in this article. If you have any complaints or copyright issues related to this article, kindly contact the provider above.
Comments
No comment