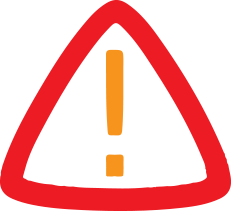
Best Practices for Optimizing Warehouse Space Utilization
(MENAFN)
Warehouse space is a valuable asset, and yet you can often feel like there’s never enough of it.
What would you say if we told you that you might not need more space? You simply need to use the room that you already have more efficiently.
Keep reading to find out how to get the most out of the square footage in your storage.
1. Asses Your Warehouse Space
Before making any changes, take a step back to assess your current warehouse setup. There’s a good chance you have untapped space that could be put to better use.
Here is what you can do:
● Measure your warehouse capacity: Don’t just focus on what is at your eye level; calculate the vertical space, too.
● Evaluate how efficient your storage is: Are shelves sitting half-empty? Do pallets have awkward gaps? Are your aisles too wide?
● Track all inventory movement: Which items fly off the shelves, and which ones collect dust? See if any “traffic jams” prevent your team from getting to the items quickly.
● Identify any dead space: Look for underused areas, such as the tops of racks, corners, and gaps between shelves.
2. Tap Into a Vertical Storage System
If you’re only using floor space, you’re missing out on a goldmine of vertical storage potential.
Here is how to maximize your vertical storage:
● Install high-riser racking systems: Pallet racking, cantilever racking, and modular shelving units allow you to stack inventory higher and increase the overall storage density.
● Use Modula vertical storage lifts: These automated storage and retrieval systems (AS/RS) are built to exploit the vertical space and reduce retrieval time.
● Implement stackable bins and pallets: Make sure all your containers are the same size and fit together perfectly so you can save in space and create a safer environment.
● Consider intermediate floors: Adding an intermediate level in high-clearance areas can double your usable space without requiring expansion.
3. Optimize Aisle Width and Layout for Efficiency
Aisles are necessary for movement and order picking, but too much space between shelves leads to wasted space.
However, shrinking them too much can cause congestion and slow down operations, so striking the middle ground can be challenging.
To optimize your aisle space, try doing the following:
● Use narrow aisle racking (NAR): Standard warehouse aisles are made with a width of around 10–12 feet so that traditional forklifts can move around. By narrowing them to 6–8 feet and using specialized forklifts, you can increase your storage capacity by up to 50%.
● Implement one-way traffic flows: Clearly marked one-way aisles prevent congestion and improve the efficiency of picking and restocking tasks.
● Adopt a zone-based layout: Keep high-demand items closer to the packing and shipping area to cut down on travel time.
4. Use a Slotting System for Inventory
With a smart slotting system, everything’s right where it should be, saving you time and making the most of your space.
To keep things organized, try following these best slotting practices:
● Group similar items together: For example, you can store garden tools together, such as shovels, rakes, and spades, so your employees know exactly where to find a certain group of items.
● Position fast-moving products up front: Store your most popular products closer to the packing and shipping area so they’re easy to grab and get out the door quickly.
● Switch things up for seasonal items: Rotate inventory based on demand. For instance, winter coats, holiday decorations, and summer gear should always be within easy reach when they’re in season. This way, they don’t get lost in the back of the warehouse when you need them most.
5. Upgrade to Smart Storage Solutions and Automation
Investing in automation pays off eventually as it can not only help you cut down on wasted space but can also reduce your labor expenses.
Consider implementing the following modern storage solutions:
● Automated storage and retrieval systems (AS/RS): These are robotic systems that automatically store and retrieve inventory, using robots or automated cranes to access high shelves and move items around.
● Mobile shelving systems: Mobile shelving systems are designed to slide together when not in use, freeing extra space. Instead of having fixed gaps between shelves, these systems move along tracks, allowing you to open only the aisle you need at any given time.
● Warehouse management software (WMS): This software keeps track of your inventory in real time, letting you know exactly where everything is. It can help you optimize your warehouse's operations by pinpointing the best locations for storage items based on factors like demand, accessibility, and size.
6. Implement Best Inventory Management Practices
Holding onto excess inventory “just in case” can clutter your warehouse and waste space. Instead, adopting lean inventory principles will help you keep stock at the right levels.
Here’s how to reduce excess inventory:
● Adopt a just-in-time (JIT) Inventory system: Order stock only when you need it, based on real-time demand.
● Regularly audit slow-moving stock: If something’s been collecting dust for months, it’s time to question whether it still belongs in your warehouse.
● Optimize supplier relationships: Work together with your suppliers on optimizing order quantities and delivery schedules based on the actual demand.
7. Standardize Storage Containers and Pallets
Stacking mismatched bins and pallets is as frustrating as trying to fit a cube into a round hole.
Here’s how to keep things tidy:
● Invest in stackable, modular bins: Opt for bins designed to stack safely upward and maximize vertical space.
● Match bins to your shelving system: Make sure your storage containers fit your rack dimensions properly to avoid wasted shelf space or unstable, hazardous stacking.
● Use color-coded or barcode labels: Assign specific colors or barcodes to different product categories so workers can quickly identify and retrieve items without digging through bins.
Wrapping It Up
Optimizing your warehouse is all about making it work smarter rather than cramming in more shelves.
Make the most of your vertical space, organize your inventory efficiently, and invest in smart storage solutions to keep everything running in sync without feeling like you’re stuck playing a never-ending game of Tetris.
Take a fresh look at your warehouse, make a few strategic tweaks, and see just how much more efficient (and spacious) it can be!
MENAFN19032025008088017206ID1109330773

Legal Disclaimer:
MENAFN provides the
information “as is” without warranty of any kind. We do not accept
any responsibility or liability for the accuracy, content, images,
videos, licenses, completeness, legality, or reliability of the information
contained in this article. If you have any complaints or copyright
issues related to this article, kindly contact the provider above.
Comments
No comment