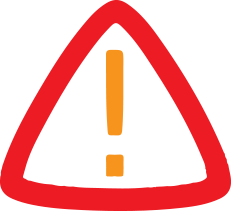
Will Humanoid Robots Make Industrial Robotic Arms Obsolete?
December 31, 2024 by David Edwards
Two of the biggest trends we have noticed and covered over the past seven years or so since we started this website have been what are called“autonomous mobile robots”, or AMRs, and collaborative robotic arms, or“cobots”, which are different from traditional robotic arms in that they do not need to be kept separate and can be used much like power tools.
Traditional industrial robotic arms were generally too dangerous to be too close to. They don't know you're there and have the power to cause injury or death if they make contact with you in the course of doing their job.
But even these“traditional” industrial robots have increasingly become more collaborative through, for example, being installed with sensors to detect human presence or touch, and stop when they might cause harm.
That's a big change brought about by the rapid adoption of collaborative robots, which were first built by Universal Robots, and slightly later by ABB. These robots were designed from the beginning to be used in close proximity with human workers.
Industry professional will, of course, know all this, but we like to think this website attracts new readers all the time who would apreciate a quick explanation of the background to what we are talking about.
The other big trend is, as mentioned earlier, autonomous mobile robots, which are the small, box-like robots on wheels which scurry around warehouses, bringing goods and shelves to a picking station where are a human will take one or more items to build and complete a customer order.
The global market for AMRs has grown at an exponential pace over the past five years or so. Companies like Geekplus emerged out of nowhere to become the billion-dollar enterprises that they are today.
Interestingly, both these new technologies – cobots and AMRs – have been combined into one new category of machine called“industrial mobile robots”, which, as you can imagine or may know, is basically the arm perched on top of the box.
This has obvious applications in a variety of sectors – picking in warehouses and inspecting in factories, to name two examples – and not only represent an evolution of robotic technology, it may actually prevent the complete paradigm change that humanoid robots are threatening to bring about.
Humanoid revolutionYes, it wouldn't be too overblown to say that humanoids are a revolutionary technology in the robotics industry, a revolution that could do away with the traditional and collaborative robotic arm as well as the AMR.
Realistically, it's still likely that cobots and AMRs will maintain their market share because what they do now are simple tasks that you don't need a complex humanoid for. And anyway, an AGV – automated guided vehicle – or even an AMR could probably still move material much faster and in larger volumes than any of the humanoids currently being developed could.
However, it is a valid question: Could industrial robotic arms be replaced by humanoid robots? Let's explore.
Managed obsolescenceThe aims of this article is not to scare manufacturers of industrial robotic arms or AMRs. Most certainly not. Maybe a little bit. But not that much. We appreciate that we have large numbers of readers in both sectors and they have the driving forces in the growth of our website.
Our intention is to help the relevant people in the industry plan for the possible changes that humanoid robots may bring about.
Let's be honest. If you can buy humanoids at a fraction of the cost of traditional industrial robots and still achieve the same amount of productivity and quality, wouldn't you do it?
Common sense or intuition would probably say yes. But let's imagine that studies show that it makes sense to switch to humanoids. What happens then?
That's for you to figure out. Our job is just write articles to help you figure out how.
General assemblyThe modern assembly line, pioneered by Henry Ford over a century ago, revolutionised manufacturing by introducing standardised workflows and mass production.
As industries grew more complex, the introduction of industrial robotic arms in the late 20th century redefined efficiency, precision, and scalability in manufacturing.
These robotic arms became indispensable in robotic work cells, performing tasks with speed and accuracy unattainable by human workers.
Today, the automotive industry remains the largest buyer of industrial robots, utilising them for tasks such as welding, painting, assembly, and material handling.
The question now arises for real, rather than merely whimsical thoughts: Could humanoid robots, with their potential for flexibility and adaptability, replace industrial robotic arms in these and other applications?
Top industrial robotic arm manufacturersHere's a list of the top industrial robot arm makers who may want to consider building humanoids of their own rather than get pushed out of markets that they have more or less owned since the 1950s and '60s – pushed out by humanoid robots made by the same tech companies that have taken over most of the rest of the economy and world. And space.
It's possible that these companies are rendered helpless. Maybe they will be unable to do anything about humanoids backed by big tech companies. Moreover, it's quite possible that their customers – especially automotive companies – will build humanoids of their own, like Guangzhou Automotive Company has and others are preparing to do.
Nonetheless, here's a list of large, traditional industrial robot makers. The estimates of the number of robots they each have in operation around the world are probably grossly underestimated, but we'll leave a more accurate count for another article. This just gives you some ball park figures.
1. Fanuc : A Japanese robotics giant with a history dating back to 1956, Fanuc is known for its high-precision CNC machines and robotic arms. With more than 750,000 robots installed globally, Fanuc dominates industries such as automotive, electronics, and logistics.
2. ABB : Based in Switzerland, ABB introduced its first electric industrial robot in 1974. Today, it has a global install base of more than 500,000 robots, offering solutions for welding, painting, and assembly lines.
3. Kawasaki Robotics : Since launching its first robot in 1969, Kawasaki has been a pioneer in industrial robotics, focusing on automotive and heavy industries. It has over 200,000 units installed worldwide.
4. Yaskawa Electric : Founded in 1915, Yaskawa's Motoman division has delivered more than 500,000 robots, specializing in welding, packaging, and assembly applications.
5. Kuka : A German robotics leader, Kuka introduced its first robot in 1973. With over 400,000 installations globally, it's a major player in automotive and manufacturing industries.
6. Staubli : Known for precision robotics, Staubli's robots are widely used in the pharmaceutical and food industries.
7. Epson Robots : Epson's SCARA and 6-axis robots are popular in electronics manufacturing and small-scale assembly.
8. Denso Robotics : As one of the largest suppliers of robots for small assembly tasks, Denso has deployed over 120,000 robots worldwide.
9. Fanuc Robotics America : A subsidiary of Fanuc, it focuses on North and South American markets, contributing significantly to the global robot count.
10. Comau : An Italian company specialising in flexible automation solutions, particularly for automotive assembly lines.
Information about the collaboratorsUniversal Robots (UR) introduced the concept of collaborative robots (cobots) in 2008, enabling robots to work safely alongside humans without extensive safety barriers.
This innovation influenced major industrial robot manufacturers to develop their own cobot lines, such as ABB's YuMi, Fanuc's CR series, and Kuka's LBR iiwa.
Cobots have opened new possibilities in small and medium-sized enterprises by handling tasks such as light assembly, inspection, and material handling with ease and adaptability.
What do you do?Industrial robotic arms excel in tasks that demand speed, precision, and repeatability, including:
- Welding : Automotive and heavy industries.
- Painting : Ensuring even coverage and consistency.
- Material handling : Lifting, sorting, and transporting.
- Assembly : Electronics, automotive, and appliances.
- Inspection : High-precision quality control.
- Packaging : Consumer goods and pharmaceuticals.
Several humanoid robots are being tested for industrial tasks, including:
- Tesla Optimus : Prototyped for material handling and assembly tasks.
- Boston Dynamics' Atlas : Showcasing advanced mobility and dexterity in experimental scenarios.
- Figure AI's Humanoid : Focused on repetitive tasks in warehouses and light manufacturing.
Humanoid robots could theoretically perform tasks like welding or painting, provided they are equipped with appropriate end effectors and precise programming.
However, their utility in industrial environments depends on their ability to match or surpass the speed, accuracy, and cost-effectiveness of robotic arms.
AMRs and IMRsAMRs, such as those developed by companies like MiR and Geekplus, have transformed warehouse operations by autonomously moving goods and shelves.
Recently, the integration of robotic arms with AMRs has created IMRs, which combine mobility and manipulation to handle complex tasks such as picking and placing.
IMRs have potential in dynamic environments but face limitations in speed and payload capacity compared to humanoids.
Humanoid ecosystemThe development of humanoid robots relies on a growing ecosystem of component manufacturers, including:
- End effector makers : Specialised grippers, tools, and welding torches.
- Sensors : Cameras, LiDAR, and tactile sensors for perception.
- Actuators : Advanced motors enabling smooth, human-like movements.
Humanoid robot prototypes are currently expensive, estimated to cost $100,000 or more. But most of the companies leading the race to bring them to market are quoting unit prices of between $15,000 and $25,000.
In contrast, the very cheapest large industrial robotic arms range from $25,000 to $100,000, depending on size and capabilities. The largest can cost upwards of $200,000.
You're fired. I'm replacing you with a cheaper and better robotWhile humanoid robots show promise, industrial robotic arms are likely to remain dominant in manufacturing for the foreseeable future due to their proven reliability, speed, and cost-effectiveness.
Humanoids may carve out niches in dynamic environments where adaptability is key.
What some might call a“realistic” timeline for significant disruption could span 10-20 years, depending on advancements in humanoid technology and cost reductions.
But that may be too optimistic from the point of view of robotic arm makers who do not diversify soon enough.
Hope in hellThe future of manufacturing may not hinge on replacing robotic arms but rather integrating new technologies like humanoid robots and IMRs into existing workflows.
Engineers and factory designers must remain adaptable, ready to embrace innovations while leveraging the strengths of established systems to optimise production.
Humanoids may currently look like hellish nightmares from Terminator films – which is probably what has kept them at bay for so long – but as more and more talented designers and engineers enter the field, the“ideal” humanoid worker is probably not as far away as we would like it to be.
Legal Disclaimer:
MENAFN provides the information “as is” without warranty of any kind. We do not accept any responsibility or liability for the accuracy, content, images, videos, licenses, completeness, legality, or reliability of the information contained in this article. If you have any complaints or copyright issues related to this article, kindly contact the provider above.
Comments
No comment