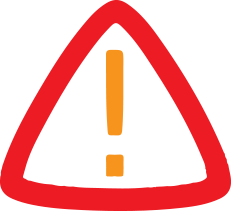
3D Printing: What Does 2025 Hold For Additive Manufacturing?
January 15, 2025 by David Edwards
Despite the tremendous success of 3D printing – also known as additive manufacturing (AM) – across many industrial sectors, the technology is still, in some ways, in its early days.
Here, a number of senior executives at 3D Systems – whose founder Chuck Hull is credited with inventing 3D printing – share their thoughts on what 2025 holds for additive manufacturing.
Dr Jeffrey Graves, president and CEOThroughout 2024, additive manufacturing has continued to demonstrate tremendous value as it's integrated into production manufacturing workflows.
As we look to the coming year, I expect we'll see adoption continue to accelerate in high reliability markets such as energy, oil and gas, semiconductor capital equipment manufacturing, and aerospace and defense.
While all of these markets operate within very exacting standards and regulatory requirements for part quality, performance, reliability, and traceability, they are in various stages of their AM journey.
One of the new markets where we are beginning to see an increased appreciation for the value of AM is semiconductor capital equipment manufacturing and data centers. Trillion-dollar investments are being made in AI that influence these areas.
The nanoscale of advanced microprocessors, combined with the extraordinary number used in a modern data center, creates an extremely challenging environment to keep the processors cool in operation.
AM is already beginning to show promise as a way to produce heat sinks using laser powder bed fusion (LPBF) and pure copper. As we progress through the coming year, I anticipate we'll see many more of these components produced to give GPU and data center architects a powerful means of removing heat effectively from the system.
While these newer application spaces are beginning to take hold, I anticipate some of the early adopters of AM such as F1 racing, foundries, and even aerospace and defense will deepen the use of the technology across their businesses.
As AM solution providers continue to bring new advancements to market - in materials, hardware, and software - I believe these precision-driven markets will evolve how they use the technology to deliver value for production applications across their manufacturing workflows.
I see tremendous opportunities in the coming year in healthcare as well. Whether we are looking at medical devices for orthopedic applications or for the dental market to align, protect, repair, and replace teeth, it is likely the trend to deliver patient-specific solutions will proliferate.
AM's ability to enable the simultaneous production of unique complex parts can help surgeons and clinicians deliver a better experience to their patients.
I expect the advancements AM has already made in these areas will also enable great strides in newer fields such as regenerative medicine over the coming months, with the potential to improve the quality of life for countless patients.
Finally, over the past 12 months, we've seen significant progress in the capability of software to not only accelerate but manage the manufacturing workflow thus transforming how products are brought to market.
As we look to 2025, I anticipate we'll see an increase of the adoption of manufacturing operating systems to provide full factory floor workflow integration, automation, control, and optimization across both industrial and healthcare markets.
The integration of these systems can help accelerate the design and production of additively manufactured parts across the entire manufacturing workflow to increase efficiency and facilitate regulatory compliance.
Dr Joe Zuiker, EVP, engineering and operationsIn 2025 and beyond, the additive manufacturing industry will continue to make inroads in various production applications. I believe the underlying 3D printing technology, materials and software will play a significant role.
For polymer printing, this progress will be driven by the unique product design capabilities that AM provides, combined with the higher productivity, producibility, and throughput of projector-based vat systems and the improving durability and performance of photopolymer materials.
I anticipate full field raster-based projector imaging systems will displace many vector-based laser applications because of the faster speed, higher throughput, and enhanced producibility advantages possible with such systems.
This transition will be at all levels of system quality and performance from low-cost prosumer printers all the way to advanced lights-out manufacturing systems. When these hardware advantages are combined with new photopolymer materials, the step forward in AM value could be remarkable in many applications.
Many new photopolymer materials have been introduced or are expected in the near future that can provide significant improvements in printed component properties including durability, strength, fire retardance, and a wide range of other properties.
Further, there has been a groundswell of academic research on advanced digital manufacturing using light-based reactions. New and novel catalyst and multi-catalyst polymers may extend the range of properties which can be created.
With better properties and potential methods of recycling, companies will likely be enticed to accelerate their digital manufacturing initiatives.
Generative design is another trend that I expect will accelerate and drive unprecedented amounts of 3D-printed products due to the complexity a fully optimized product will need.
For example, the geometric needs of 3D-printed tissues and organs are driving innovations in computer science that will find their way to commercial and industrial products.
We are already seeing the results of some of the advanced research into bioprinting being incorporated into industrial projector-based systems and should expect even more in the near future.
Reji Puthenveetil, EVP, additive solutions and chief commercial officerThe additive manufacturing (AM) industry continues to transition from generalized manufacturing to solutions that are tightly aligned with specific, high-impact needs. I believe this will continue to accelerate as we move into 2025.
Investment casting is a process that has existed for thousands of years. AM has made some in-roads, yet the technology has struggled to adequately compete with traditional processes due to material costs being significantly higher than injection molding.
Recently, new solutions have come to light that leverage 3D printing's inherent strengths to produce hyper-efficient 3D-printed casting patterns that make AM more cost-competitive with traditional manufacturing.
I anticipate this will enable foundries to more readily embrace AM, helping to expand their business, not only by increasing the speed at which they can produce patterns, but also their ability to increase the volume of work they can take on to drive additional revenue.
In the aerospace and defense sector, we are seeing continued growth within parts that are in limited production or discontinued, yet are still required for maintenance, repair and overhaul (MRO) activities.
AM can help rapidly increase production capacity, with lower technical barriers to entry. I believe the coming year will build upon that.
I expect this to occur not only for the production of end-use parts, but also for casting of molds and patterns, as well as manufacturing aids such as jigs, tools and fixtures. This is all incremental to the other opportunities within the sector presented by new designs enabled by additive.
High-performance computing (HPC) applications demand significantly more power and thermal management for industrial data processing, data centers, and hosting applications further escalate these requirements.
This necessitates large-scale rack-based systems with complex networking, storage, redundancy, power supply, and thermal solutions to handle the heat generated by numerous HPC modules.
As semiconductor and high-performance electronics push the limits of thermal management, precision, and space efficiency, I believe AM will enable a new era of products with tailored thermal solutions, such as ultra-efficient heat sinks and custom cooling channels that optimize each device's unique performance needs.
In healthcare, AM's impact on patient-specific medical devices has been profound. As we enter the new year, I expect we'll continue to see a sharpened focus on the use of AM to produce patient-specific devices for applications such as craniomaxillofacial, orthopedic oncology, spinal fusion surgeries, and total joint reconstruction.
With the addition of FDA-cleared AM solutions such as the ability to 3D print PEEK; I anticipate the number of types of implants that use this technology to grow, delivering significant benefits to surgeons and patients.
Similarly in the dental industry, AM has already demonstrated its ability to accelerate the production of trays, models, surgical guides, dentures, orthodontic splints, retainers, crowns, and bridges.
As AM solution providers enhance the capabilities of 3D printing technologies and materials, I expect to see an increase in the number of applications in which we can use the technology to address the alignment, protection, repair, and replacement of teeth.
Legal Disclaimer:
MENAFN provides the
information “as is” without warranty of any kind. We do not accept
any responsibility or liability for the accuracy, content, images,
videos, licenses, completeness, legality, or reliability of the information
contained in this article. If you have any complaints or copyright
issues related to this article, kindly contact the provider above.
Comments
No comment