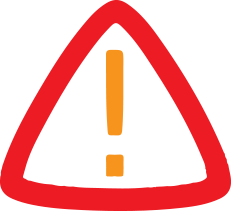
Tungsten Carbide Dies Grinding
The grinding of tungsten carbide dies is typically performed using diamond wheels, which are capable of cutting through the hard material with ease. The use of diamond wheels ensures that the grinding process is both efficient and effective, minimizing the risk of damage to the dies. Additionally, the grinding process must be carefully controlled to prevent overheating, which can cause thermal damage to the tungsten carbide material. Coolants are often used during the grinding process to dissipate heat and maintain the integrity of the dies.
One of the key challenges in tungsten carbide dies grinding is achieving the required surface finish. The surface finish of the dies is critical to their performance, as it affects the quality of the final product. A smooth and polished surface finish is essential for reducing friction and wear during the forming or drawing process. Achieving this level of precision requires a combination of skilled operators, advanced grinding equipment, and meticulous attention to detail.
In addition to surface finish, the dimensional accuracy of the tungsten carbide dies is also crucial. The dies must be ground to exact specifications to ensure that they produce components with the desired dimensions and tolerances. This requires precise measurement and control throughout the grinding process. Advanced metrology tools, such as coordinate measuring machines (CMMs), are often used to verify the dimensions of the dies and ensure that they meet the required standards.
Tungsten Carbide Tool GrindingTungsten carbide tool grinding is another essential process in the manufacturing industry, particularly for tools used in machining and cutting applications. Tungsten carbide tools, such as end mills, drills, and inserts, are known for their exceptional hardness and wear resistance, making them ideal for high-performance machining. The grinding process for these tools involves shaping and sharpening the tungsten carbide material to achieve the desired cutting geometry and edge quality.
The grinding of tungsten carbide tools is typically performed using diamond grinding wheels, similar to the process used for tungsten carbide dies. The use of diamond wheels ensures that the grinding process is efficient and effective, allowing for the precise shaping of the tools. Additionally, the grinding process must be carefully controlled to prevent overheating and thermal damage to the tungsten carbide material. Coolants are often used during the grinding process to dissipate heat and maintain the integrity of the tools.
One of the key challenges in tungsten carbide tool grinding is achieving the required cutting geometry. The cutting geometry of the tools is critical to their performance, as it affects the cutting efficiency, tool life, and surface finish of the machined components. Achieving the desired cutting geometry requires a combination of skilled operators, advanced grinding equipment, and meticulous attention to detail. The grinding process must be carefully controlled to ensure that the tools are ground to the exact specifications required for their intended applications.
In addition to cutting geometry, the edge quality of the tungsten carbide tools is also crucial. The edge quality of the tools affects their cutting performance and wear resistance. A sharp and well-defined cutting edge is essential for efficient machining and long tool life. Achieving this level of precision requires advanced grinding techniques and equipment, as well as skilled operators who can carefully control the grinding process.
Tungsten Carbide Tool SharpeningTungsten carbide tool sharpening is a vital process in maintaining the performance and longevity of cutting tools. Over time, the cutting edges of tungsten carbide tools can become dull and worn, reducing their cutting efficiency and increasing the risk of tool failure. Sharpening the tools involves the removal of material from the cutting edges to restore their sharpness and cutting performance. This process requires specialized equipment and techniques to ensure precision and efficiency.
The sharpening of tungsten carbide tools is typically performed using diamond grinding wheels, which are capable of cutting through the hard material with ease. The use of diamond wheels ensures that the sharpening process is both efficient and effective, minimizing the risk of damage to the tools. Additionally, the sharpening process must be carefully controlled to prevent overheating, which can cause thermal damage to the tungsten carbide material. Coolants are often used during the sharpening process to dissipate heat and maintain the integrity of the tools.
One of the key challenges in tungsten carbide tool sharpening is achieving the required edge quality. The edge quality of the tools is critical to their performance, as it affects the cutting efficiency, tool life, and surface finish of the machined components. Achieving a sharp and well-defined cutting edge requires a combination of skilled operators, advanced sharpening equipment, and meticulous attention to detail. The sharpening process must be carefully controlled to ensure that the tools are sharpened to the exact specifications required for their intended applications.
In addition to edge quality, the dimensional accuracy of the tungsten carbide tools is also crucial. The tools must be sharpened to exact specifications to ensure that they produce components with the desired dimensions and tolerances. This requires precise measurement and control throughout the sharpening process. Advanced metrology tools, such as coordinate measuring machines (CMMs), are often used to verify the dimensions of the tools and ensure that they meet the required standards.
Nail Making Tool GrindingNail making tool grinding is a specialized process in the manufacturing industry, particularly for tools used in the production of nails. Tungsten carbide nail making tools, such as punches and dies, are known for their exceptional hardness and wear resistance, making them ideal for high-performance nail production. The grinding process for these tools involves shaping and sharpening the tungsten carbide material to achieve the desired geometry and edge quality.
The grinding of nail making tools is typically performed using diamond grinding wheels, similar to the process used for other tungsten carbide tools. The use of diamond wheels ensures that the grinding process is efficient and effective, allowing for the precise shaping of the tools. Additionally, the grinding process must be carefully controlled to prevent overheating and thermal damage to the tungsten carbide material. Coolants are often used during the grinding process to dissipate heat and maintain the integrity of the tools.
One of the key challenges in nail making tool grinding is achieving the required geometry. The geometry of the tools is critical to their performance, as it affects the efficiency and quality of the nail production process. Achieving the desired geometry requires a combination of skilled operators, advanced grinding equipment, and meticulous attention to detail. The grinding process must be carefully controlled to ensure that the tools are ground to the exact specifications required for their intended applications.
In addition to geometry, the edge quality of the nail making tools is also crucial. The edge quality of the tools affects their performance and wear resistance. A sharp and well-defined edge is essential for efficient nail production and long tool life. Achieving this level of precision requires advanced grinding techniques and equipment, as well as skilled operators who can carefully control the grinding process.
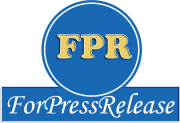
Legal Disclaimer:
MENAFN provides the information “as is” without warranty of any kind. We do not accept any responsibility or liability for the accuracy, content, images, videos, licenses, completeness, legality, or reliability of the information contained in this article. If you have any complaints or copyright issues related to this article, kindly contact the provider above.
Comments
No comment