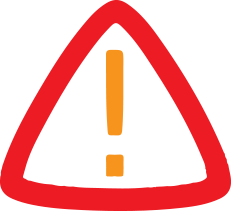
Building Zambian Homes With Local Materials Delivers Benefits That Imports Don't: Study
Traditionally, buildings were constructed by local craftspeople, from readily available materials. The result was buildings which were highly suited to local contexts, cultures and climates.
Modern building materials and regulations changed that. Today, most buildings are made of materials such as cement and steel. In African countries that don't make these products themselves, this means that many building materials and components are imported.
Read more: Hemp is more sustainable than timber – here's how it could transform low-carbon construction
I'm an architect who researches environmental design and sustainable built environments. I worked with a team on Zambia's Green Jobs programme . This project aimed to produce more and better jobs in work that benefited the environment.
The team I was part of used a Sustainable Building Assessment Tool that I had developed to determine how local building materials could be used by medium and small enterprises in Zambia's building construction sector to become more sustainable. This tool also emphasises the use of local building materials in housing developments.
We compared housing that was built with no preference for local materials with alternative and local construction approaches. Our research found that the way new housing developments are designed and built can create social and economic benefits at a local level, especially if they focus on using local building materials .
Urban housing projects and imported materialsBuildings based on local content are those where the planning, designing, constructing, repairing, maintaining and deconstructing support the use of local materials and components. This includes instances where imported raw material is converted into products made locally.
The Green Jobs Programme built five alternative housing designs and compared these to a conventional urban house.
This house was built using mainly imported materials. Courtesy Jeremy Gibberd
In a conventional urban house, we found that a large proportion of the components were imported. The imported components included:
-
roof materials: pressed aluminium roof sheeting
roof structure: steel trusses ceiling: suspended panels
light and electrical fittings: imported kitchen units: fibreboard
windows: aluminium doors: pressed steel
flooring: tiles.
One of the houses made with local materials. Courtesy Jeremy Gibberd
The alternative housing designs set out to mainly use local content. Most of the materials used to build them were made and sourced locally in Zambia:
-
roof materials: concrete tiles
roof structure: timber trusses from local sustainably managed forests ceiling: plasterboard
light and electrical fittings: local and imported windows and doors: hardwood timber from local sustainably managed forests
walls: compressed earth blocks made from material excavated on site.
The research showed that if a housing project focused on using local content, more than 90% of the capital costs for new buildings could be spent in the local economy.
We calculated this by measuring the value of local materials and components as a proportion of the total material and component cost of the project. This allowed us to determine the percentage value of local content in the construction materials and products.
We also found that using local content would potentially support a diversified economy which is more resilient. This is because when there is a demand for a diverse range of locally made building components and materials, these local economies become more resilient than those that rely mainly on imports, and only produce one or two products locally.
For example, a town that only has a concrete block manufacturing plant would be very negatively affected by a downturn in this sector. A town with window, door, furniture, truss, tile and insulation manufacturing plants would be more resilient as only one sector would be affected.
Buying local materials for housing developments benefits the local economy. For example, our project involved small businesses made up of local carpenters who make high quality hardwood windows from timber grown in sustainable Zambian forests. Jobs were created and skills were developed.
The environment was also protected because there was no need to transport windows by truck from distant places. Carbon emissions were avoided. We also found that the alternative buildings were more attuned to their contexts and climate. For example, earth construction draws on local traditional skills and provides for cooler, more comfortable indoor environments than lightweight imported materials.
How the costs compareLocal, small-scale manufacturers of building materials can't always produce these materials at a lower price than mass-produced imported materials. But there is a broader set of potential economic benefits associated with buying local materials and components.
Buildings with high levels of local content fund local manufacturing and generate taxes which support the local economy and improve quality of life. On the other hand, buildings that use mainly imported components result in money leaving the country and do not support local development or generate taxes.
Taxes paid by ordinary people are used by government to build infrastructure and buildings, such as universities, schools, clinics and police stations. Using local content in buildings generates more taxes that can be used to improve education, health and quality of life.
Read more: How investing in green buildings, including cheaper home loans, is a win for banks, people and our planet
Using local materials can also make it cheaper for building owners to adapt, repair and maintain their buildings. This is because the skills and materials required for this are locally available and there are no delays waiting for imported material to arrive.
What needs to happen nextUsing local materials for building needs to be encouraged. New housing developments should be seen as part of a circular economy – where local goods are used, recycled, and repaired in an environmentally friendly way.
Local content projects need to be scaled up and coordinated. Countries would benefit from a framework that sets out how government and private developers should use local content in buildings. New building regulations and standards might be needed to enable local and traditional materials to be safely used in buildings.
Read more: If companies want net-zero carbon offices, they need to focus on building materials
Training for architects and other built environment professionals is also needed. This will improve awareness and build the skills needed for integrating locally produced components and materials into buildings.
The main emphasis needs to be on developing a thriving manufacturing and construction sector that uses local content.
(Zambia's Green Jobs programme was managed by the United Nations Environment Programme , the International Labour Organisation and the government of Zambia.)


Legal Disclaimer:
MENAFN provides the information “as is” without warranty of any kind. We do not accept any responsibility or liability for the accuracy, content, images, videos, licenses, completeness, legality, or reliability of the information contained in this article. If you have any complaints or copyright issues related to this article, kindly contact the provider above.
Most popular stories
Market Research
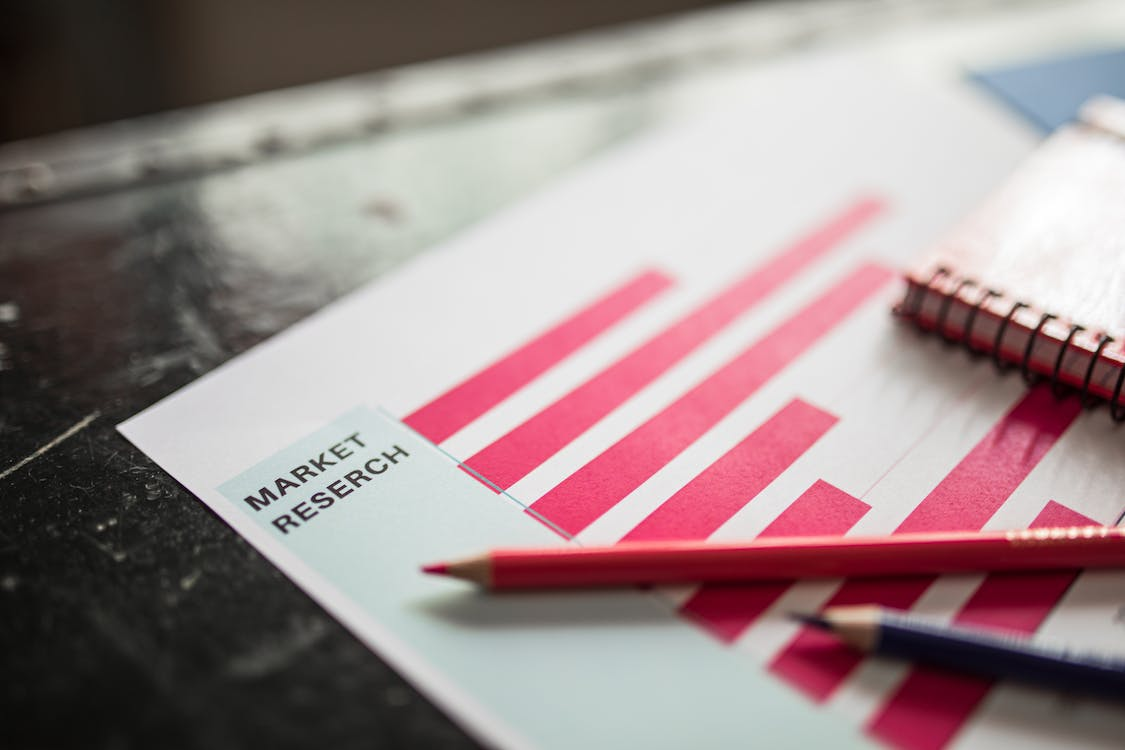
- Manuka Honey Market Report 2024, Industry Growth, Size, Share, Top Compan...
- Modular Kitchen Market 2024, Industry Growth, Share, Size, Key Players An...
- Acrylamide Production Cost Analysis Report: A Comprehensive Assessment Of...
- Fish Sauce Market 2024, Industry Trends, Growth, Demand And Analysis Repo...
- Australia Foreign Exchange Market Size, Growth, Industry Demand And Forec...
- Cold Pressed Oil Market Trends 2024, Leading Companies Share, Size And Fo...
- Pasta Sauce Market 2024, Industry Growth, Share, Size, Key Players Analys...
Comments
No comment