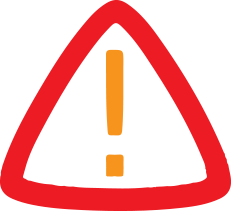
Star Refrigeration's Dr Dermot Cotter To Present Latest Research On Industrial Refrigeration Energy Efficiency At IOR Techtalk
Drawing from detailed surveys of twenty industrial sites across the food, drink, chemical and pharmaceutical sectors, the study reveals significant opportunities for energy efficiency improvements and reduced emissions from refrigeration equipment.
Dr Dermot Cotter, said, "Our findings indicate two key opportunities to reduce energy consumption and carbon emissions in industrial refrigeration equipment. First, through improved system design specifications that prioritise energy efficiency from the outset, and second, by transforming how we maintain existing systems. Instead of just focusing on keeping systems running, maintenance should proactively optimise energy use."
The study particularly emphasises the findings related to the Chemical and Pharmaceuticals (C&P) sectors which represent 10.9% of the UK manufacturing turnover, and the food and drink manufacturing sector, which accounts for 17% of the total turnover of all UK manufacturing activity, with over 60% of food in the UK relying on the cold chain.
The presentation will offer attendees valuable insights into current energy usage patterns, technological adoption trends, and the effectiveness of maintenance practices across these vital industrial sectors. Findings from the study reveal that while the core refrigeration technologies-compressors, condensers, expansion valves, and controls-are consistent across industries, evaporator types vary significantly based on specific applications. These applications range from votators and plate freezers to fin and tube heat exchangers used for air cooling.
The study also examines how refrigerant selection impacts carbon emissions, identifying opportunities for sustainable improvements. The industrial refrigeration systems surveyed were found to employ Ammonia (R717), Carbon Dioxide (R744), Propane (R290), and various Hydrofluorocarbons (HFCs), including R134a, R404A, R407A, R410A, R417A, R422D, R449A, and R453A.
The study found that many industrial refrigeration sites have substantial energy-saving potential, primarily through better maintenance and equipment optimisation. In ten out of fourteen sites with air-cooled condensers excessive fouling was reported, leading to increased energy consumption. Routine maintenance measures, such as keeping condensers clean, and proactive monitoring were some of the simple practices highlighted to effectively reduce compressor power consumption by up to 26%.
Despite of the potential benefits of using data for maintenance or efficiency optimisation, only five sites had sub-metering of the refrigeration systems in place. While these sites tracked cumulative electrical usage, none utilised sub-metering as part of their maintenance strategy. One exception was Site 13, which had a refrigeration optimisation system in just one chiller, leveraging a digital twin to assess and monitor the performance of sub-components within the refrigeration system.
The paper also delves into the significant energy savings achievable by optimising evaporating temperatures in industrial refrigeration, stating that currently, many suppliers provide process equipment with standard evaporating temperatures but do not emphasise the efficiency gains from slight modifications to suit unique production requirement on site. For example, many freezing applications are designed with an evaporating temperature of -38°C, yet increasing this to -35°C could reduce compressor energy consumption by 11.6%. This suggests that re-evaluating standard design specifications and making relatively small adjustments to equipment setup can significantly improve efficiency, reduce carbon emissions, and lower operational costs.
The TICR project provides valuable data and benchmarks for the refrigeration sector, equipping businesses with the tools they need to optimise their energy use and carbon footprint. The complete findings and detailed recommendations for end users in the manufacturing sector will be published by the TICR project in March 2025, alongside a technology roadmap for emissions reduction.
For more information about the IOR TechTalk presentation, to register, and to download the paper, visit TechTalk - Energy Usage in the Industrial Refrigeration Sector
SOURCE Star Refrigeration
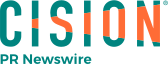
Legal Disclaimer:
MENAFN provides the information “as is” without warranty of any kind. We do not accept any responsibility or liability for the accuracy, content, images, videos, licenses, completeness, legality, or reliability of the information contained in this article. If you have any complaints or copyright issues related to this article, kindly contact the provider above.
Most popular stories
Market Research
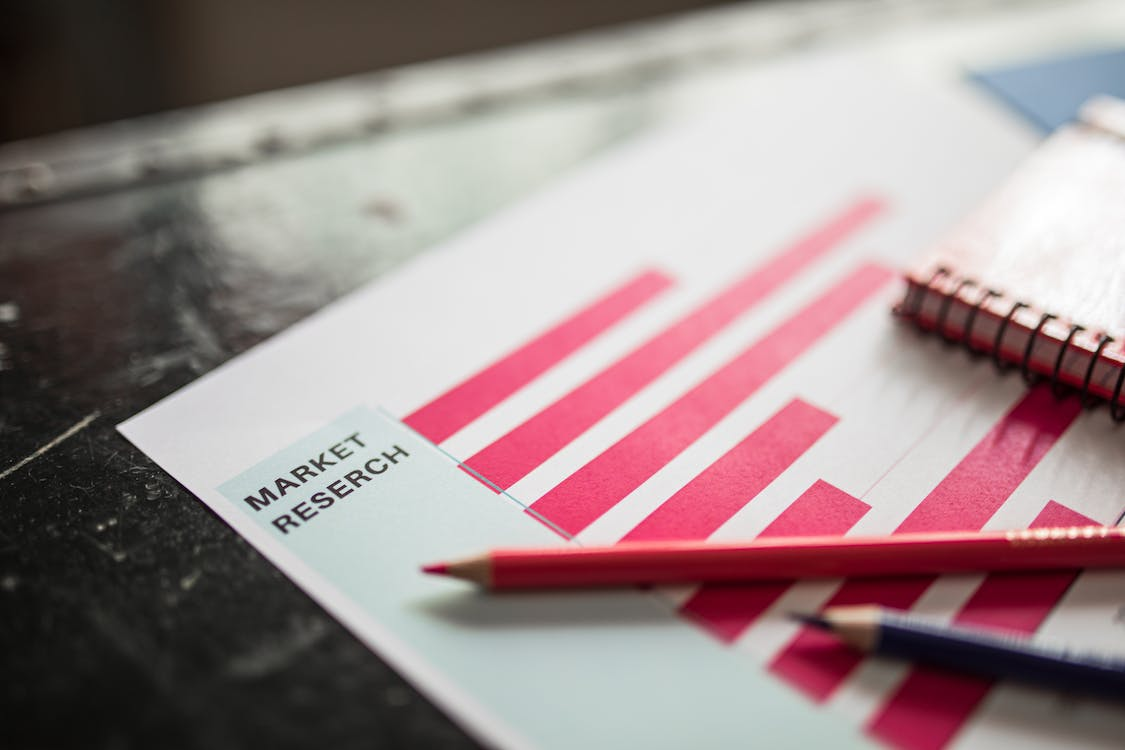
- Manuka Honey Market Report 2024, Industry Growth, Size, Share, Top Compan...
- Modular Kitchen Market 2024, Industry Growth, Share, Size, Key Players An...
- Acrylamide Production Cost Analysis Report: A Comprehensive Assessment Of...
- Fish Sauce Market 2024, Industry Trends, Growth, Demand And Analysis Repo...
- Australia Foreign Exchange Market Size, Growth, Industry Demand And Forec...
- Cold Pressed Oil Market Trends 2024, Leading Companies Share, Size And Fo...
- Pasta Sauce Market 2024, Industry Growth, Share, Size, Key Players Analys...
Comments
No comment