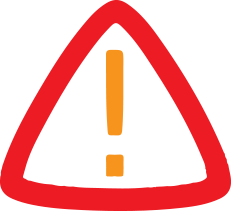
Microshells' Melody: Tuning Into The Vibrations Of Tiny Tech
Schematic of a doubly curved elastic material-imperfect FGM microshell. FGM, functionally graded material.
GA, UNITED STATES, December 31, 2024 /EINPresswire / -- Researchers have unveiled groundbreaking insights into the complex vibrations of tiny, curved shells crafted from functionally graded materials (FGMs). These microshells, integral to micro-electromechanical systems (MEMS ) and biomedical devices, exhibit distinct behaviors at the microscale due to their unique composition and dimensions. By delving into factors such as material composition, material imperfections, and structural scale, the study marks a pivotal step toward designing more efficient and reliable microsystems, where mastering frequency responses is essential for optimal performance.
Functionally graded materials (FGMs), characterized by their gradual variation in properties across one or multiple directions, have transformed modern engineering, offering enhanced resistance to thermal and mechanical stresses. However, at the microscale, inherent porosity-or tiny voids-within these materials presents challenges by altering their structural integrity and vibrational dynamics. Traditional models often fall short in capturing these intricate behaviors, creating an urgent need for advanced analytical frameworks to predict the vibrations of FGMs microshells. Such advancements are critical to their practical deployment in cutting-edge technologies.
This challenge inspired a collaborative effort by researchers from the University of Adelaide, the University of Canberra, and Westlake University. Published (DOI: 10.1002/msd2.12137 ) in the International Journal of Mechanical System Dynamics on December 9, 2024, the study examines the vibrational behavior of FGM microshells, highlighting the influence of material composition, material imperfections, and small-length scale coefficients on their frequency responses.
Breaking new ground, the research utilizes a sophisticated five-parameter shear deformable model to analyze the free vibrations of doubly curved imperfect FGM microshells. The study introduces a modified power-law rule, capturing the uneven logarithmic distribution of porosity through the microshell's thickness, to better account for material imperfections. Using Hamilton's principle, the researchers derive precise motion equations for these complex structures. Their findings illuminate how material composition, material imperfections, and microscale effects converge to shape the dynamic behavior of microshells. This nuanced understanding serves as a blueprint for optimizing microsystems, particularly in next-generation micro-electromechanical systems (MEMS) and biomedical applications.
Lead researcher Dr. Behrouz Karami emphasized the study's importance:“Our research unravels the intricate interplay between material composition, porosity, and microscale effects on FGM microshells' dynamics. This understanding is pivotal for developing high-performance microsystems, especially in fields like MEMS and biomaterials, where precise material properties are non-negotiable.”
The study's implications extend far and wide, offering a roadmap for designing advanced MEMS devices and biomaterials. By mastering the vibrational properties of these microshells, engineers can create structures that are lighter, stronger, and more resilient under real-world conditions. This knowledge promises to drive innovation across critical sectors, including automotive, and medicine, where high-performance, lightweight components are essential for achieving both efficiency and safety.
DOI
10.1002/msd2.12137
Original Source URL
Lucy Wang
BioDesign Research
email us here
Legal Disclaimer:
EIN Presswire provides this news content "as is" without warranty of any kind. We do not accept any responsibility or liability for the accuracy, content, images, videos, licenses, completeness, legality, or reliability of the information contained in this article. If you have any complaints or copyright issues related to this article, kindly contact the author above.
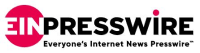
Legal Disclaimer:
MENAFN provides the information “as is” without warranty of any kind. We do not accept any responsibility or liability for the accuracy, content, images, videos, licenses, completeness, legality, or reliability of the information contained in this article. If you have any complaints or copyright issues related to this article, kindly contact the provider above.
Most popular stories
Market Research
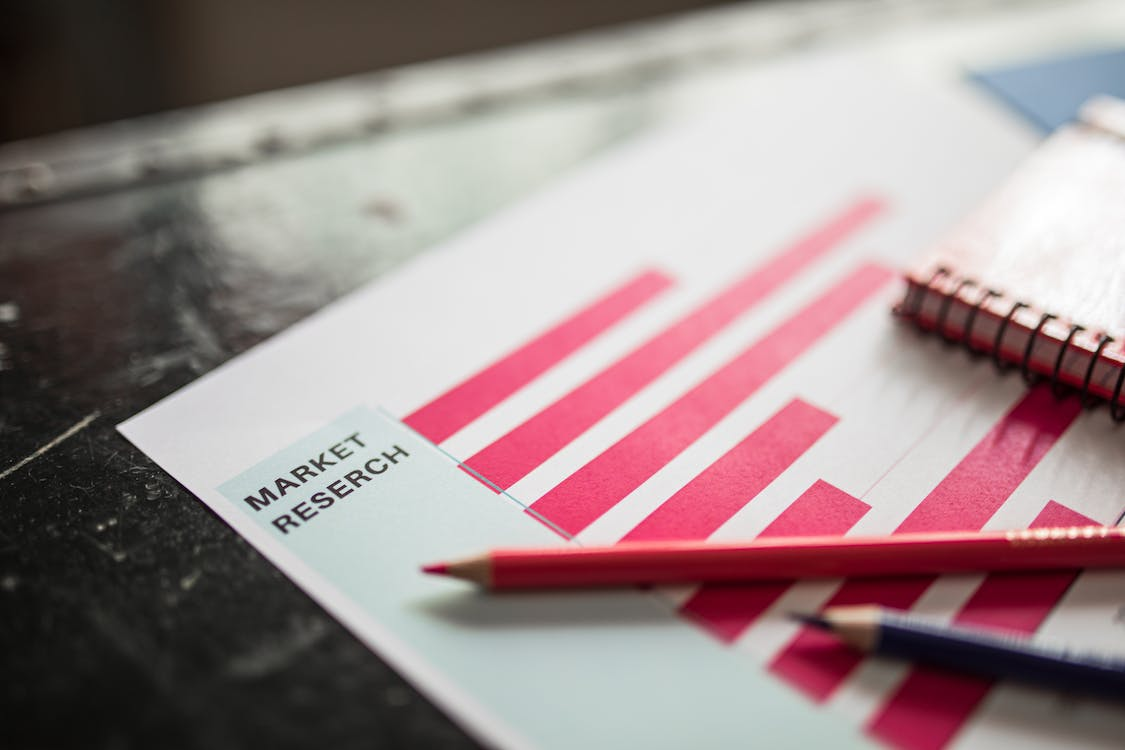
- Manuka Honey Market Report 2024, Industry Growth, Size, Share, Top Compan...
- Modular Kitchen Market 2024, Industry Growth, Share, Size, Key Players An...
- Acrylamide Production Cost Analysis Report: A Comprehensive Assessment Of...
- Fish Sauce Market 2024, Industry Trends, Growth, Demand And Analysis Repo...
- Australia Foreign Exchange Market Size, Growth, Industry Demand And Forec...
- Cold Pressed Oil Market Trends 2024, Leading Companies Share, Size And Fo...
- Pasta Sauce Market 2024, Industry Growth, Share, Size, Key Players Analys...
Comments
No comment