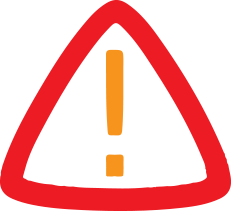
How Manufacturing Leaders Can Thrive When Entering New Markets
December 22, 2024 by David Edwards
By Shinichiro Nakamura , president of one to ONE Holdings
Global expansion accounts for more than half of all corporate growth in the past decade. So, it's no surprise that manufacturers continue to penetrate new markets.
This wider globalization trend is largely driven by the rise of emerging markets, sustainability efforts, and localizing production based on resources.
However, entering new markets is easier said than done, particularly when facing hurdles such as regulations, tariffs, talent shortages, different cultures, and limited technology.
These threats can severely undermine manufacturing capabilities across regions, and it's crucial that organizational leaders are aware of risks and opportunities to overcome them.
Let's dive into these.
Understanding regional differencesIt's essential to remember that global trends will underpin regional ones, and therefore, manufacturers must keep an eye out for them. To illustrate, the competition and dynamic between China and the US usually have widespread ramifications for manufacturing around the world.
To start, pricing often varies significantly across regions. Steel tends to be cheaper in Asia than in Europe and North America. However, experts are forecasting that these price gaps will shrink in the wake of China's surplus supply of cheap steel.
Another factor to examine is the level of demand for products in a particular region. That means examining the degree of competition within a market and the consumption behaviors of relevant industries.
A useful way to gauge a product's market performance is to look at sector specialization. Regions often specialize in manufacturing sectors that align with local resources and expertise.
For example, China is renowned for its electronics manufacturing, and cities like Shenzhen are regarded as hubs for tech companies and assembly operations.
Facing challenging shiftsNo two markets are exactly alike when it comes to regulations, and navigating these can be a complex challenge for manufacturers expanding.
These regulations and laws can span industry-specific requirements to broader business operation laws, often covering areas such as licensing and compliance, tariffs and trade barriers, data protection and privacy, and employment laws.
Political and economic changes can suddenly impact regulations, leading to uncertainty and a lack of clarity around compliance. For instance, with Donald Trump returning to the presidential office, there's widespread speculation that international trade tariffs will soar in the US.
This could greatly impact manufacturers in certain industries that have operations and businesses in the US. To avoid legal pitfalls, organizations should invest in local expert guidance to help ease the process of understanding regulatory requirements and ensuring full compliance with them.
Tackling logistics is another challenge manufacturers face. First, they have to source new reputable suppliers and vendors that ensure continued smooth operations. This can be particularly tricky without an established network to recommend these, which can result in a lot of trial and error.
To save time and resources, manufacturing companies should maximize their network or look to branch out ahead of time so getting the ball rolling with those suppliers and vendors is easier once they're ready to set up shop in the new market.
Geopolitical instability is another vital consideration that is hugely impacting trade around the world. The Houthi attacks on vessels in the Red Sea, for instance, have been blocking what's described as one of 'the world's trade arteries', causing congestion in ports across Europe and Asia.
Bolstering a risk management plan by assessing the likelihood of such threats and their potential damage to operations within a specific area is key to maximizing supply chain resilience and mitigating the extent of logistical disruption.
Available resources and technologies within a country can also hugely impact logistics and operations for manufacturers. Specifically, technology use can be limited by regulations and accessible talent to operate these, causing further adjustment pains for manufacturers entering new markets.
It's useful to pre-assess resources and technology capabilities within a region before, and keeping an inventory of this can help manufacturing leaders plan their operations accordingly.
This is especially important for manufacturers looking to make the most of data-driven operations to enable them to efficiently allocate practice and procedure management across multiple factory locations.
Managing cultural differencesConsidering culture is inevitable when an organization expands beyond borders. First and foremost, establishing central corporate values, such as a mission statement, can be transformative to aligning teams and departments within a company.
In fact, a strong brand identity that sets the tone of the corporate culture is one of the best ways to unite people and foster an environment of collaboration between teams.
Training and development initiatives can help bring corporate culture to life. Nurturing a drive for growth among employees and acknowledging their efforts through rewards and incentives can really fuel positive behaviors like cross-collaboration and innovation.
Having that central identity and culture makes a powerful north star for employees across an organization, regardless of their roles and responsibilities, because it pluralizes the employment experience while recognizing individual efforts.
Additionally, the adage that communication is key is hugely applicable to cross-cultural management. Invest in effective communication channels that empower connectivity between teams across locations to prevent isolation and siloing. Platforms such as Slack have proven game-changing for many organizations around the world.
This should also include regular one-on-one meetings between leaders and their teams to continually strengthen communication and motivate collaborative approaches.
This also helps managers identify any grievances or suggestions around operations, business processes, and the general employee experience, making sure team members feel seen and heard.
However, sometimes, individuals need an extra helping hand when dealing with cross-cultural differences in communication. Generative AI can be incredibly useful for helping people better understand the nuances of different cultures and languages, lowering the risk of misinterpretation.
Every challenge is an opportunity for growth, and recognizing the implications of regional and cultural differences and regulatory changes is a critical first step to effectively preparing for global expansion.
Understanding how these hurdles affect operations and business processes will help leaders solidify risk management plans for maximal agility according to the unique requirements of each region and market.
About the author : Shinichiro Nakamura is the president of one to ONE Holdings , a group of companies which includes Daiwa Steel Tube Industries , one of the most innovative galvanized steel tube manufacturing companies in the world. Founded in 1932, Daiwa Steel Tube Industries produces around 60,000 tons of in-line galvanized steel tubing annually for scaffolding, frames for greenhouse, roller conveyers, and other structural/mechanical tubing for various applications.
Legal Disclaimer:
MENAFN provides the
information “as is” without warranty of any kind. We do not accept
any responsibility or liability for the accuracy, content, images,
videos, licenses, completeness, legality, or reliability of the information
contained in this article. If you have any complaints or copyright
issues related to this article, kindly contact the provider above.
Comments
No comment