Wesco 2024 Sustainability Report: Health & Safety
Health and Safety
Dedication to Safety Excellence
We work hard to keep each other safe. It is the first tenet in our core value of commitment to our people. In our commitment to health and safety, we strive
for zero incidents and continuously work towards reducing associated risks. This dedication is reflected in our comprehensive approach to improvement, encompassing dedicated programs, employee best practice sharing, and extensive training initiatives.
Health and Safety Management System
At the core of our safety efforts is a robust health and safety management system covering all internal work- related functions across our facilities, customer locations and corporate offices. This systematic approach involves assessing risks, implementing controls, evaluating their effectiveness, and acting on identified trends through preventative and responsive measures. Our tracked metrics provide valuable insights for the ongoing performance of our health and safety program. They include near miss reporting, training completion statistics, injury rates and data from key initiatives like ergonomic wearable feedback.
The oversight of our health and safety management system is entrusted to our global corporate safety team, ensuring a cohesive and standardized approach. Every employee plays a pivotal role in contributing to our enterprise-wide safety performance objectives, with individual contributions and actions being closely measured. Aligned with OHSAS-18001 and ISO-45001 guidelines, our health and safety program include the following.
Social Goals
Target: Achieve a 15% reduction in Total Recordable Incident Rate (TRIR) by 2030 from a 2020 baseline.
Progress: Met in 2022; 2023 TRIR was 0.5 (6% increase from baseline)*
Target: Provide 425,000 hours of safety training and development to our employees by 2030 .
Progress: 292,033 hours of safety training completed
*While our TRIR increased 6% from the baseline, it is favorable to the industry average. Data available by NAICS code for 2022 shows the applicable industry average TRIR of 2.3; Wesco's TRIR of 0.5 is favorable to the industry benchmark.
Monitoring and Continuous Improvement
The vigilance of our global corporate safety team is maintained through performance reviews with key leadership, daily interactions with operations leaders, routine KPI reviews, and regular facility audits to verify compliance. Further reinforcing our commitment, each location benefits from a dedicated regional health and safety advisor responsible for overseeing local leadership, ensuring compliance, conducting routine facility audits, evaluating training needs, planning training calendars, and tracking, trending, and reporting on health and safety metrics.
In 2023, Wesco relaunched our Safety Committee initiative featuring an updated charter and Safety Committee member training. Safety Committees have been implemented at all Regional Distribution Centers, with a target to include all Regional Distribution Centers and Branches in 2024.
- Management and Supervisory Responsibilities: Define specific protocols for management to support involvement with the program.
Employee Responsibilities: Outlines the health and safety rules employees are expected to follow.
Accident Investigation Processes: Establishes process to be followed in the event of an accident or near miss.
Enforcement Procedure: Provides a system of actions and outlines steps to be taken if health and safety policies aren't followed.
Reporting of Safety Concerns: Offers a means for employees to provide input to the health and safety program suggesting any preventative considerations.
Safety Committee Systems: Outlines the framework of a site safety committee, including the layout of an agenda, membership and method for taking minutes.
New Employee Orientation: All employee's complete health and safety training as part of their orientation and introduction to their facility.
Regulatory Compliance: Ensures we communicate relevant information on legal and other requirements to our employees and other interested parties.
Risk and Incident Management
We employ a robust risk management process to eliminate potential hazards before anyone becomes sick or injured while at work. Our employees assess work areas for hazards or safety risks and when identified, promptly report them, enabling rapid rectification of potential risk or hazards by supervisors. All employees have the right to challenge any unsafe work situation, and they can do so anonymously. When unsafe work conditions are reported, an evaluation is conducted, and the employee is notified of the action taken to address the situation.
At each location, monthly safety inspections are conducted using a checklist of key hazards and risks. This checklist is regularly updated to include new hazard awareness trends as they emerge. Meanwhile, managers are informally inspecting working activities for safety hazards on an ongoing basis. When a near-miss occurs, reports are used to create awareness of the conditions or behaviors that can be corrected to prevent future incidents. Lastly, an emergency action plan is reviewed and updated regularly. The plan includes current contact information, logged drills and facility response. In the event of an incident-no matter how minor-we require that it be reported promptly to the frontline supervisor for investigation and evaluation.
Since every incident includes a sequence of contributing risks, it may be possible to avoid a repeat of the first event by recognizing and eliminating these risks. The removal of even a single risk may prevent a recurrence. Our supervisors are trained in incident investigation procedures and techniques, such as the“five whys”- the practice of asking why repeatedly to discover the root cause of an issue-to begin gathering data and understanding what hazards existed and what controls may have failed or may not have existed. Robust documentation protocols ensure event information can be fully vetted and reviewed by business leadership and the location's health and safety advisor, with a strong focus on corrective action plans. Once the contributing factors and/or root causes have been determined, the corporate health and safety advisor will communicate a global safety alert with the corrective actions taken to prevent the occurrence in any other facility. Corrective actions may address risk assessments, standard operating procedures, design changes for working conditions, ergonomics, engineering controls, retraining for equipment and hazards knowledge, and ensuring compliance with regulations and standards.
Site Inspections and Audits
Facility managers conduct workplace inspections at least once a month and cover all areas where employees, visitors, or contractors could be expected to access. Managers or supervisors at each site also informally observe work activities for safety hazards. They do so as part of their daily safety Gemba walks-a workplace walkthrough aiming to identify potential risks-as a routine function of their daily activity.
Safety – Branch and Distribution Center
A large portion of Wesco employees work in branch locations or distribution centers. Their primary duties are receiving, picking, packing and shipping materials. The high-risk elements of our business identified through the analysis of historical safety data and internal risk assessments are forklift tasks, ergonomic risks from manual material handling and slips, trips and falls.
To minimize the risk of injury, we have implemented innovative technologies, such as wearable devices. The utilization of wearable technology has resulted in a significant reduction in hazards per hour related to manual work stressors.
Wesco has improved our employee safety education systems, format and content to address these hazards going forward. We require all warehouse employees to undergo targeted training on safe lifting techniques, ergonomically safe lifting limits, mechanical assistance, or team lift for heavy objects. These efforts limit manual material-handling risk.
To minimize injuries relating to slips, trips and falls, we established a risk management plan that identifies, assesses, controls and monitors relevant hazards.
All warehouse employees are trained to stop any unsafe practices or correct any unsafe conditions relating to slips, trips and falls.
Highlight: In 2023, Wesco's internal audit team identified inadequate training and documentation of training for Powered Industrial Truck (PIT) operators. After this discovery, we introduced a company-specific PIT Training Program and began providing“train-the-trainer” courses to create a pool of Wesco-Authorized PIT Trainers.
To learn more, download the 2024 Wesco Sustainability Report here.
About This Report
Unless otherwise stated, this report covers activities, data and initiatives from our fiscal year 2023.
ESG Disclosure and Framework Alignment
The topics covered in this report include those that we have determined to be material for our business and stakeholders as noted on page 12. Wesco aligns with several ESG frameworks and disclosures in support of our commitment to transparency and our fulfillment of stakeholder needs and expectations. We leverage the following frameworks and standards to provide robust ESG information disclosure:
- Global Reporting Initiative (GRI): GRI offers a list of global standards and guidelines around sustainability reporting.
Sustainability Accounting Standards Board (SASB): SASB provides a comprehensive set of industry-specific disclosure topics and guidelines.
Task Force on Climate-Related Financial Disclosures (TCFD): TCFD provides disclosure recommendations on thematic ESG topics such as governance, strategy, risk management, metrics and targets to provide stakeholders with fuller information surrounding climate risks.
CDP: Formerly the Carbon Disclosure Project, CDP is an international organization that helps companies and cities measure and disclose important environmental impact information through an annual questionnaire and rating system.
United Nations Global Compact (UNGC): UNGC is an initiative that aims to help businesses align their strategies and work toward the U.N.'s Sustainable Development Goals.
United Nations Sustainable Development Goals (U.N. SDGs): U.N. SDGs provide a shared set of 17 toward peace and prosperity for people and planet goals and create a call to action by all countries in a global partnership.
We also regularly engage with our investors, employees, customers, regulators, ratings agencies and others on ESG and business issues. Additional information about Wesco can be found in our public financial filings-including our annual report and proxy filings-as well as on the Security and Exchange Commission's website at or on the Investors page of our website at Wesco.
Wesco plans to continue to report annually as we monitor, measure, and deepen our ESG initiatives and disclosures.
Wesco endorses the United Nations Sustainable Development Goals (SDGs), which are a call to action to end poverty, protect the planet, and ensure that all people enjoy peace and prosperity.
More information about our SDG aligned initiatives is included throughout this report.
Assurance
We did not seek third-party assurance for this report; however, we will consider doing so for future reporting. The information and data contained in this report was vetted by internal subject matter experts on the various ESG topics included in this report.
Contact Us
We appreciate and welcome feedback on our ESG initiatives and reporting and invite you to contact us directly via email at ....
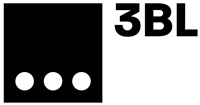
Legal Disclaimer:
MENAFN provides the
information “as is” without warranty of any kind. We do not accept
any responsibility or liability for the accuracy, content, images,
videos, licenses, completeness, legality, or reliability of the information
contained in this article. If you have any complaints or copyright
issues related to this article, kindly contact the provider above.
Most popular stories
Market Research

- 1Inch Unlocks Access To Tokenized Rwas Via Swap API
- What Is The Growth Rate Of The Europe Baby Food And Infant Formula Market In 2025?
- BTCC Announces Participation In Token2049 Singapore 2025, Showcasing NBA Collaboration With Jaren Jackson Jr.
- Ecosync & Carboncore Launch Full Stages Refi Infrastructure Linking Carbon Credits With Web3
- New Silver Launches In California And Boston
- United States Fin Fish Market Size Forecast With Demand Outlook 20252033
Comments
No comment