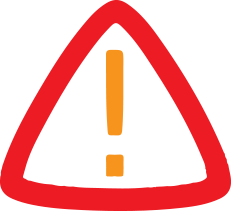
Dental Implants And Prosthetics Contract Manufacturing Market To Worth Over US$ 3.23 Billion By 2033 | Astute Analytica
Market Forecast (2033) | US$ 3.23 billion |
CAGR | 8.5% |
Largest Region (2024) | North America (36%) |
By Product Type | Dental prosthetics (62%) |
By End Use | Dentistry Companies (55%) |
Top Drivers |
|
Top Trends |
|
Top Challenges |
|
Core Materials and Breakthrough Techniques Elevating Dental Contract Production
Materials selection lies at the heart of successful dental implants, and contract manufacturers in the dental implants and prosthetics contract manufacturing market have scaled up to meet stringent demands for quality, biocompatibility, and long-term durability. At a specialized facility in the United Kingdom, BEGO processes around 2,500 titanium rods monthly, transitioning these into complex implant fixtures using five-axis CNC machining. Scheftner, known for high-performance alloys, runs three advanced electron beam melting (EBM) stations exclusively for titanium and cobalt-chrome. Meanwhile, Argen's additive manufacturing suite in San Diego operates 10 selective laser melting (SLM) machines simultaneously, layering metal powders to create implant abutments with intricate geometric tolerances. Zirconia frameworks, milled by at least six dedicated workstations at Zirkonzahn in Italy, undergo carefully calibrated sintering cycles that exceed 1,450 degrees Celsius, ensuring the final products exhibit robust fracture resistance. In an emerging trend, Polyether Ether Ketone (PEEK) has gained momentum; some independent labs utilize up to 1,200 PEEK blanks per quarter to craft lightweight, temporary restorations for implant cases.
Such production feats are complemented by advanced digital engineering, blending subtractive and additive approaches that accommodate the complexities of individual patient anatomies in the dental implants and prosthetics contract manufacturing market. Multiple contract manufacturing hubs now integrate dynamic 3D scanning, capturing up to 5 million data points in a single dental-arch scan to ensure unmatched precision. This wave of technological progress underscores why large dental companies no longer view outsourcing as a compromise but rather as a route to guaranteed consistency. From custom abutments shaped via 3D-printed wax patterns to fully milled zirconia crowns, these processes align with strict mechanical and aesthetic requirements demanded by discerning clinicians. Historically, small-scale milling setups lacked the resources to manage such cutting-edge tools, but specialized contract manufacturers can justify the high acquisition and maintenance costs. In doing so, they help unify the entire manufacturing pipeline-raw material sourcing, advanced CAM software usage, finishing, and packaging-into a well-orchestrated flow. The outcome is an end product capable of seamlessly integrating into the oral environment, backed by the reliability and expertise of manufacturing experts whose everyday business is perfecting each step of the fabrication journey.
Leading Industry Players and their Collaborative Strategies With Dental Contract Manufacturers
Industry stalwarts and niche specialists in the dental implants and prosthetics contract manufacturing market alike form close alliances with contract manufacturing partners, recognizing that knowledge sharing and logistical coordination drive superior outcomes. Straumann, for example, harnesses at least four external milling centers across Europe and Asia, collectively delivering over 15,000 customized abutments monthly. Nobel Biocare's collaboration with select 3D printing facilities in California results in complex restorative components that undergo final polishing in-house before distribution. Meanwhile, Ivoclar Vivadent leans on contract partners to produce roughly 2,100 pressed ceramic restorations daily, focusing its own resources on R&D and clinical validation. Ziterion, based in Germany, handles zirconia milling tasks for more than 70 laboratories, employing a rotating staff of 65 specialists who oversee uninterrupted production shifts. Some mid-size providers concerned with castable alloys, like Scheftner, maintain six induction casting machines that cater exclusively to implants with angled screw channels.
These collaborations thrive on sophisticated digital workflows, anchored by advanced design libraries that guarantee compatibility between brand-owner CAD frameworks and the contract manufacturer's toolchain. At times, special jigs or fixtures must be built to handle custom angles or undersized diameters. Precision levels can dip below 5 microns in certain multi-unit prosthetic cases, a feat rarely matched by smaller labs operating alone. Hence, clinics benefit from final products that mirror the brand's hallmark design ethos while still being produced in high-volume runs by external milling centers. Many of these centers in the dental implants and prosthetics contract manufacturing market also hold ISO 13485 certifications, alongside additional international clearances such as MDR compliance for distribution in European markets. This robust quality stance cements trust among major players like Dentsply Sirona, which sources specific metal frameworks from partners that maintain eight or more distinct finishing stations. The resulting synergy highlights how contract manufacturers not only absorb labor-intensive production cycles but also ensure brand designs reach the patient precisely as intended. Together, these alliances push the entire dental industry toward a collaborative future, where best-in-class technology fuses with clinical insight to produce restorations and implant components that match the patient's unique physiology.
Quality Management, Regulatory Compliance, and Specialized Services Driving Outsourcing Decisions
Reliability underpins every contract manufacturing agreement, prompting stringent controls across each phase of production. Many facilities rely on automated coordinate measuring machines (CMMs) that measure objects with an accuracy within 2 microns, confirming that thread patterns, internal connections, and external geometries perfectly align with design specs. Cleanroom-class assembly areas, often certified at ISO Class 7 or 8, minimize airborne contaminants that can compromise implant coatings or polished surfaces. Bicon Dental Implants audits its partners at least twice per year, verifying compliance with device labeling requirements and testing protocols for each batch of implant fixtures. Similarly, some contract manufacturers conduct up to 120 routine calibrations annually on laser sintering machines to maintain optimal heat flow and layering accuracy. Detailed device tracking is essential, with product barcodes allowing clients to trace the exact machining station, operator ID, and batch number in case of quality queries.
Global regulations in the dental implants and prosthetics contract manufacturing market also fuel this rigor, requiring constant vigilance and procedural refinement. FDA-approved facilities must maintain Design History Files (DHFs), storing every revision, acceptance test, and engineering change notice relevant to a particular implant model. In practical terms, this can mean each contract manufacturing partner holds tens of thousands of pages of documentation for multiple clients and device variations. MDR obligations in the European Union impose additional layers of oversight, prompting producers to maintain thorough clinical evaluations. Consequently, an ISO 13485 certification often forms the baseline requirement for these vendors, confirming their Quality Management System meets sector standards. In pursuit of specialized tasks, certain contract firms boast in-house test rigs able to handle 48-hour cyclical loading, simulating repetitive chewing forces on abutments and crowns. Others run dedicated laser etching stations for product identification, an essential service for custom restorations requiring unique barcodes. Altogether, these multifaceted measures foster confidence among dental manufacturers eager to ensure consistent quality, mitigate liability concerns, and expedite the path from design validation to clinical application. Thus, contract manufacturing becomes not only a cost-effective solution but also a well-regulated ecosystem where reliability, documentation, and specialized capabilities secure the longevity of each implant and prosthetic outcome.
Learn more about this report before you buy:
Key Clinical Advantages and Comprehensive Value Offered By Contract-Produced Implants
Patients and practitioners alike reap tangible benefits from the expertise and resourcefulness of contract manufacturing. In Switzerland, clinicians working with abutments produced by milling centers such as Etkon typically report improved integration rates, attributing success to the precise sub-5-micron tolerances achieved on internal connections. Over 2,000 clinics across Asia dental implants and prosthetics contract manufacturing market order specialized angled abutments from Narval Dental Services, allowing custom solutions for patients with compromised bone angles. Meanwhile, some North American groups, like Apex Dental Milling, process an average of 300 zirconia frameworks daily that can be delivered to clinics in under three days. For full-arch restorations, advanced digital scans capturing at least 1 million data points ensure that final components achieve intimate adaptation with minimal chairside adjustments. By lowering the margin for error, contract manufacturing helps reduce post-operative complications, leaving patients with stable, comfortable restorations.
Cost and accessibility figure prominently in this value equation too. The average dental laboratory might store 15 different milling burs just to handle the variety of possible implant and prosthetic workflows. By outsourcing to a contract service that stocks 80 or more specialized tools, clinicians in the dental implants and prosthetics contract manufacturing market can accommodate complex cases-such as narrow diameter implants or multi-unit bridges-without heavy capital outlay. Furthermore, contract manufacturers upgrade their machinery at fixed intervals, with some adopting new five-axis systems every 18 to 24 months to stay current on milling efficiency and precision. This ensures the hardware used to create each implant is state-of-the-art, a level of technological currency that many smaller labs cannot maintain. The immediate benefit of reduced overhead, combined with robust clinical outcomes, underscores why contract manufacturing has become such a strong pillar of the modern dental industry. Ultimately, the synergy among design expertise, global production capacity, and stringent quality controls guides a process that consistently delivers top-tier implants and prosthetics, granting a lasting, comfortable restoration experience grounded in the latest engineering innovations.
Global Dental Implants And Prosthetics Contract Manufacturing Market Major Players:
- ARCH Medical Solutions Corp BIOPLATE Cendres+Métaux MedTech Elos Medtech AB Halder GmbH Micron Products INC. SteriPackGroup Tectri SA Wesley Coe Ltd YOMURA Other Prominent Players
Key Segmentation:
By Product
- Dental Implants
- Titanium Implants Zirconium Implants
- Bridges & Crowns Dentures Abutments
By End-Use
- Medical Device Companies Dentistry Companies
By Region
- North America Europe Asia Pacific Middle East & Africa (MEA) South America
Tailor this report to your preferences:
About Astute Analytica
Astute Analytica is a global analytics and advisory company which has built a solid reputation in a short period, thanks to the tangible outcomes we have delivered to our clients. We pride ourselves in generating unparalleled, in depth and uncannily accurate estimates and projections for our very demanding clients spread across different verticals. We have a long list of satisfied and repeat clients from a wide spectrum including technology, healthcare, chemicals, semiconductors, FMCG, and many more. These happy customers come to us from all across the Globe. They are able to make well calibrated decisions and leverage highly lucrative opportunities while surmounting the fierce challenges all because we analyze for them the complex business environment, segment wise existing and emerging possibilities, technology formations, growth estimates, and even the strategic choices available. In short, a complete package. All this is possible because we have a highly qualified, competent, and experienced team of professionals comprising of business analysts, economists, consultants, and technology experts. In our list of priorities, you-our patron-come at the top. You can be sure of best cost-effective, value-added package from us, should you decide to engage with us.
Contact Us:
Astute Analytica
Phone: +1-888 429 6757 (US Toll Free); +91-0120- 4483891 (Rest of the World)
For Sales Enquiries: ...
Website:
LinkedIn | Twitter | YouTube


Legal Disclaimer:
MENAFN provides the information “as is” without warranty of any kind. We do not accept any responsibility or liability for the accuracy, content, images, videos, licenses, completeness, legality, or reliability of the information contained in this article. If you have any complaints or copyright issues related to this article, kindly contact the provider above.
Comments
No comment