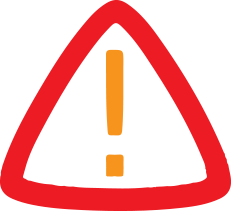
On The Road To Decarbonization: The Importance Of The Electric Arc Furnace Route In Steel Production Robotics & Automation News
The steel industry is facing an epochal challenge: decarbonization. With growing pressure to reduce greenhouse gas emissions and the need to mitigate climate change, steel manufacturers must find alternative ways to make their production more environmentally friendly.
In this context, the electric arc furnace route is becoming increasingly important and promises a more sustainable future for the steel industry.
Traditionally, steel has mainly been produced by the blast furnace route, which is based on smelting iron ore with coke. However, this process is extremely energy-intensive and results in significant CO2 emissions. In response, the Electric Arc Furnace (EAF) route has gained popularity in recent years.
This still innovative approach (the first patents were filed as early as 1878) uses electricity to produce steel from scrap or directly reduced iron, drastically reducing CO2 emissions.
The blast furnace route still has to follow this path and requires considerable investment for this transformation, which is only feasible with government support.
The desired method has not yet been tested on an industrial scale and it remains to be seen whether the required qualities can be offered at competitive prices.
On a smaller scale, in so-called direct reduction plants, it works. Here, the iron ore is reduced by natural gas; in future, this is to become green hydrogen, which from today's perspective contributes to very considerable costs.
The process, known as direct reduction, has been known for a long time and has hardly been used in the past precisely because of its enormous costs.
At this point, the question of distortion of competition must also be asked? Since the blast furnace route receives very high subsidies to enable it to use a technology that the electric arc furnace route has been using successfully for a long time, the question of balance arises.
The EAF route must also shoulder considerable costs as part of the transformation in order to maintain and expand its prominent role in the CO2 balance of steel manufacturing companies and thus make its contribution to reducing emissions.
We cannot and do not want to stand still on this route either and the question must be allowed as to why the state does not support those who are technologically ahead?
One example is the Swiss Steel Group with its plants in Switzerland, Germany, France, the USA and Canada, which has decided to make the electric arc furnace route its main production route.
Incidentally, it is also the winner of this year's German Sustainability Award. Probably the most important award of its kind in Europe.
By using electric arc furnaces in all of their plants, they can produce their steel without the use of coal or coke, resulting in significant savings in greenhouse gas emissions. Only the electrodes are made of graphite and the slag is foamed with carbon wire.
But here too, work is already underway on emission-saving innovations. For example, electrode cooling and foaming using recycled plastic.
In addition, the flexibility of this process enables the efficient use of recycled scrap as a raw material, which contributes to the circular economy and reduces dependence on iron ore from environmentally harmful open-cast mining.
In 2022, for example, the company recycled 2.0 million to. of scrap were recycled by the company in 2022, making it one of Europe's leading recycling companies.
One more thing about the flexibility of the electric arc furnace route. Its great advantage is that the furnace can be switched off. A blast furnace has to run 24/7. This means you can react to fluctuating demand and energy situations and adjust production.
This also applies to surpluses in the grid. The EAF route can also relieve the grid of peaks by using its furnaces in a targeted manner. A point that is worth being seen and evaluated much more clearly by the public.
Scrap, a valuable raw materialScrap is the basis of the electric arc furnace route and is therefore a very important and valuable raw material. Steel is not consumed, but is used again and again. The circular economy leads to greater resource efficiency.
The question therefore arises as to whether a region such as Europe should not build up scrap reserves in the same way as we do with other systemically important raw materials.
This would also be a response to the increasing demand for scrap in Europe and on the global market and could contribute to greater price stability.
However, scrap also offers another major opportunity to reduce the CO2 footprint in the production of high-alloy and stainless steels. We are increasingly moving away from pure primary alloys such as ferronickel, ferromanganese or ferromolybdenum in favor of high-alloy scrap from the outset.
In the case of high-performance steels in particular, the proportion of alloying additions sometimes exceeds 30 percent. These, in turn, are particularly energy and CO2 intensive in their procurement.
It will therefore become increasingly important to alloy with quality scrap instead of pure metals in the future. The use of primary alloys cannot be completely avoided, especially for some special grades with specific requirements.
However, in order to further reduce Scope 3 emissions, both metallurgical and recycling technology innovations are required. The metallurgical laboratory of the Swiss Steel Group at Ugitech in Ugine, France, has been making a name for itself in this field for years.
One of the innovations developed there is the Ugi`Ring project, which is being worked on together with regional partners.
The 10-year, government-funded project will help to reduce the need for primary alloys, thereby increasing the company's competitiveness and further reducing the CO2 footprint of the material used.
The aim is to create the world's first“circular” steelworks in which the company's own secondary alloys are produced from waste products such as batteries, catalytic converters and similar materials. This will also make the company independent of primary alloy supplies from politically unstable producer countries.
The energy mix makes the differenceAs a rule, the steelworks on the electric arc furnace route use the energy mix that is available to them in their respective area at reasonable prices.
However, it is also possible to specifically purchase only electricity from renewable energy sources, which in turn has a drastic effect on the CO2 footprint of the material that is produced in these steelworks.
For example, the Swiss Steel Group 's Green Steel Climate+ quality has a CO2 footprint that is up to 83% lower than the global average for steel production.
Swiss Steel Group's decision to go down the electric arc furnace route reflects the change in the steel industry as a whole. More and more companies are recognizing the need to rethink their production processes and pursue more environmentally friendly alternatives.
Frank Koch, CEO of the Swiss Steel Group, says:“This paradigm shift is not only a response to regulatory requirements, but also an act of corporate responsibility towards society and future generations.”
In order to underpin the strategic decision to decarbonize, the company has therefore also joined the Science Based Targets Initiative (SBTi) with the aim of validating the roadmap for further decarbonization this year.
The SBTi has also developed a Net-Zero Standard for companies. This provides a clear and science-based definition of net zero and is a world-first framework in the private sector for setting long-term, ambitious and science-based net zero targets. These are to be achieved by 2050.
The Swiss Steel Group is one of the very few steel manufacturers in the world to have joined the Carbon Disclosure Project. The CDP project is a non-profit organization founded in London in 2000. Its aim is for companies to provide each other with transparency about their emissions in order to be able to determine the most accurate values possible across the entire value chain.
So the electric arc furnace route has already come a long way. In fact, it is currently the only one where you can already reliably produce green steel for every application and buy green steel every day, but there is still a lot to do to achieve the other goals.
In particular, the availability of affordable and sustainable electricity and the development of more efficient electric arc furnace technologies are crucial factors for its long-term success. Ensuring competitiveness is the order of the day. Short-term changes in grid charges can have a major impact.
Consortia PPAs, for example, could provide a solution here. In any case, cooperation between governments, industry and research institutions is essential in order to overcome these and other obstacles and drive forward the decarbonization of the steel industry.
Overall, the electric arc furnace route represents a promising way to decarbonize steel production. At the moment, it is absolutely leading the way. By using innovative technologies and sustainable practices, steel manufacturers like the Swiss Steel Group will take a leading role in the fight against climate change.
It is now up to the entire industry to follow this path consistently and shape a sustainable future for the steel industry. For further information, please do not hesitate to contact us.
Legal Disclaimer:
MENAFN provides the information “as is” without warranty of any kind. We do not accept any responsibility or liability for the accuracy, content, images, videos, licenses, completeness, legality, or reliability of the information contained in this article. If you have any complaints or copyright issues related to this article, kindly contact the provider above.
Comments
No comment