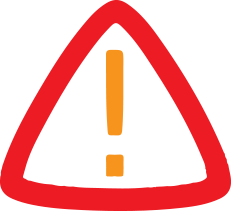
Common Ground: Are Autonomous Mobile Robots In Warehouses The Same As Autonomous Road Cars?
January 8, 2025 by Mark Allinson
For a long time, I've been wondering if an autonomous mobile robot – those small wheeled boxes you see moving shelf units and other items in warehouses – could be increased in size, then fitted with a car chassis and body, with a couple of seats inside, and marketed as a road-going, passenger-carrying autonomous vehicle.
Yes, of course, some serious design refinements of the sketched out idea above would be required and a torrent of regulations would have to be navigated, but beyond that, the internal technologies would not need to change much because, fundamentally, they are the same. Right? Or not?
Actually, I don't know. I'm not an engineer. But from what's called a high-level perspective, both AMRs and autonomous vehicles are essentially the same thing or at least perform the same function – carry goods and people around autonomously.
But let's look at the details. It may be useful for companies operating in either or both fields – although I can't think of any companies that operate in both. The only exception I can think of is BMW, which produced an AMR in-house, but then spun it off as a separate business unit.
I am, of course, talking about idealworks , which is still a BMW subsidiary company – part of the BMW Group. Which, in terms of business, means BMW is operating in both sectors. But the idea that AMRs and autonomous cars are the same and one machine can be transformed into another and vice versa is probably not a sensible notion on my part.
Press picture from BMW showing an idealworks autonomous mobile robot
Nonetheless, let's take a look at the technological similarities between the two vehicles because I've got a feeling that it's only a matter of time before the big companies in the AMR space – such as Locus Robotics, Seegrid, or Geekplus – start thinking about moving into the autonomous road vehicle space, and vice versa.
Or maybe a particularly adventurous investor or entrepreneur could buy or start an AMR company and turn it into a company that makes autonomous vehicles for every environment. It's possible. Or am I dreaming?
Autonomous futureAutonomous driving is fast becoming one of the most transformative areas of modern engineering, capturing the imagination of technology enthusiasts, investors, and consumers alike.
In parallel, autonomous mobile robots (AMRs) are making strides in warehouses and large facilities, quietly revolutionising logistics and supply chain operations.
While these applications may seem worlds apart – one navigating public roads at high speeds, the other manoeuvring through warehouse aisles – their underlying technologies are surprisingly similar.
From wheels to advanced sensors like LiDAR, both road-going autonomous vehicles and AMRs rely on a range of common components and systems to achieve safe and efficient navigation.
In this article, we'll look at some of the key technological overlaps between autonomous vehicles on roads (and large facilities like airports) and AMRs used in warehouses.
We'll explore the potential for cross-pollination of ideas and hardware – from sensor development to software suites – and consider how companies operating in one domain may venture into the other.
We'll also discuss the exciting career opportunities these overlaps create for engineers and technologists, before speculating on how the lines between autonomous road vehicles and AMRs might blur in the future.
Common technologies and componentsBelow is a list of 12 components and systems commonly found in both autonomous vehicles on roads and the smaller, wheeled AMRs that navigate warehouses.
While the scale and specific implementation of these technologies may differ, their underlying principles often remain the same.
1. Wheels and TiresPerhaps the most obvious shared feature is the presence of wheels. Whether it's a car cruising down the highway or a small robot moving a shelf around a warehouse, both require wheels designed for traction and stability.
The materials used – rubber compounds, metal wheel rims, and specialized treads – differ based on the environment but serve a similar purpose: reliable movement and support.
2. Chassis and materialsThe basic structural framework is another parallel. Autonomous cars often have steel or aluminium chassis, sometimes with composite materials to reduce weight without compromising strength.
AMRs, on the other hand, may use steel, aluminium, or high-grade plastics for their frame to balance durability and cost. Both rely on sturdy, lightweight designs to house sensors, batteries, and other components securely.
3. Electric motorsWhile internal combustion engines still exist in many road vehicles, the trend in autonomous driving is toward electric or hybrid powertrains for better control and easier integration with onboard electronics.
AMRs are almost exclusively electric, typically using brushless DC motors for torque and precise control. The principles behind electric propulsion – motor drivers, controllers, and battery management – are shared across both domains.
4. Battery systemsEnergy storage is a fundamental challenge for any untethered vehicle. Electric cars employ larger battery packs (often lithium-ion) to power not just the propulsion but also the vast array of sensors and onboard computers.
AMRs, though smaller, use similar battery chemistries, with an emphasis on quick swapping or charging to minimize downtime. Advances in battery energy density and charging technology in one sector frequently flow into the other.
5. LiDAR sensorsLiDAR (Light Detection and Ranging) has become synonymous with advanced autonomous navigation. High-end autonomous cars frequently feature LiDAR arrays to create detailed 3D maps of their surroundings in real-time.
Many AMRs also use LiDAR for mapping and obstacle detection, though they may opt for smaller, lower-cost units.
Sensor suppliers have been continually developing more compact and affordable LiDAR systems, benefiting both road vehicle and warehouse robot manufacturers.
6. Cameras and computer visionCameras – both monochrome and colour – play an integral role in object detection, navigation, and understanding a vehicle's environment. For road vehicles, camera arrays assist in lane keeping, traffic light detection, and pedestrian avoidance.
AMRs also utilize cameras (often with fish-eye or wide-angle lenses) for real-time navigation and barcode or QR-code scanning.
The underlying computer vision algorithms – image segmentation, object classification, and tracking-are similar, with each sector learning from the other's developments.
7. Radar and ultrasonic sensorsRoad vehicles typically use radar for long-range detection of other cars, while many also have ultrasonic sensors for close-range obstacle detection and parking assistance.
AMRs often rely on shorter-range radar or ultrasonic sensors to avoid collisions with shelving units, walls, and personnel.
The basic principle – sending out a signal and measuring the reflection – remains the same, though the frequencies and range requirements may differ based on application.
8. Collision avoidance systemsSafety is paramount in both industries, albeit at different scales. In autonomous cars, collision avoidance involves complex algorithms that integrate LiDAR, camera data, and radar signals to anticipate potential accidents with pedestrians or other vehicles.
AMRs similarly combine sensor inputs – often from LiDAR, ultrasound, or bump sensors – to automatically stop or reroute when encountering obstacles.
These advanced control systems rely on robust software logic to ensure reliable, real-time responses in dynamic environments.
9. Connectivity and communicationFrom 5G networks to dedicated short-range communications (DSRC), the ability to communicate is central to advanced autonomous systems on roads.
Vehicles use connectivity for real-time updates on traffic, weather, and map data. AMRs likewise utilize Wi-Fi or other wireless protocols to coordinate with warehouse management systems.
Over-the-air (OTA) updates, cloud-based analytics, and teleoperation capabilities are also becoming standard in both domains, highlighting the importance of robust networking solutions.
10. Localisation and mappingGPS is a mainstay for road vehicles, enabling precise localisation at a city scale. Although GPS can be less reliable indoors, AMRs use other localisation technologies, such as SLAM (Simultaneous Localisation and Mapping) and fiducial markers, to navigate.
The principles of high-precision mapping – updating maps in real-time, handling dynamic changes in the environment – are shared, meaning improvements in one sector can inspire or directly benefit the other.
11. Machine learning and artificial intelligenceAt the heart of any autonomous system is the software that turns sensor inputs into decision-making power. Both autonomous cars and AMRs use machine learning techniques for object detection, path planning, and anomaly detection.
Although the datasets differ – cars must recognise pedestrians, traffic lights, and lane markings, while AMRs identify shelves, pallets, and human operators – the core architectures of these AI models (for example, convolutional neural networks, reinforcement learning algorithms) often overlap, allowing lessons learned in one area to be applied in the other.
12. Safety and redundancyRedundant systems – dual power supplies, backup sensors, and fail-safe mechanisms – are crucial in both fields.
Regulatory requirements for road vehicles demand a high level of safety redundancy, but large facilities like airports and major warehouses also have stringent safety standards.
Whether a robot must perform an emergency stop if a sensor fails or a car must switch to a backup processor, the concept of fail-operational design is integral to both environments.
Opportunities for cross-pollinationThe presence of these shared components highlights a significant potential for cross-pollination between the two sectors.
Sensor suppliers, particularly those developing LiDAR, camera modules, and radar units, may find it advantageous to design products that can be scaled up or down to serve both road vehicles and warehouse AMRs.
This approach broadens the market for their products and offers economies of scale, spurring competitive pricing and more rapid technological improvements.
For software developers, advances in AI algorithms for computer vision, sensor fusion, and path planning in one domain can be adapted to the other with relative ease.
The basic physics of motion, along with the challenges of detecting objects and avoiding collisions, are widely applicable.
For instance, improved AI frameworks for object recognition in autonomous cars could be adapted to identify and categorize various types of goods in a warehouse environment.
Career opportunities for engineersThe overlap in hardware and software solutions means engineers can more easily move between the autonomous driving and warehouse robotics sectors.
Embedded systems specialists, sensor experts, computer vision engineers, and AI researchers are in high demand in both industries.
A professional specialising in LiDAR integration for self-driving cars could transition to designing sensing solutions for AMRs without completely reinventing their skill set.
This mobility not only widens the talent pool for companies but also empowers individual engineers to diversify their experience.
By working on different types of autonomous systems, professionals can gain a deeper, more holistic understanding of robotics and automation – experience that can be extremely valuable as the industry continues to evolve and combine technologies.
Future convergenceIt is not difficult to imagine a scenario in which a company currently excelling in AMRs decides to apply its expertise to autonomous road vehicles, or vice versa.
While the regulatory hurdles for on-road systems are more stringent, a strong track record in indoor navigation, path planning, and safety protocols could provide a significant head start.
Conversely, companies in the automotive sector may find new opportunities in logistics, supplying smaller-scale versions of their advanced sensor suites and control software to the world of AMRs.
Such cross-sector innovation could accelerate the pace of technological advancement and reduce costs, benefiting everyone from manufacturers to end-users.
More efficient AMRs in warehouses could bring down logistics costs, while more capable self-driving cars could enhance mobility and safety on the roads.
If these two markets continue to learn from each other, we can expect improvements in reliability, performance, and affordability across the board.
Exciting timesAutonomous road vehicles and AMRs may appear to operate in vastly different environments, but they share a remarkable array of core technologies – wheels, materials, sensors, AI software, and more.
This common ground creates ample opportunity for cross-pollination, with sensor suppliers, software developers, and robotics engineers all standing to benefit from knowledge transfer between the two fields.
For professionals, the synergies expand the range of potential career paths, allowing them to pivot between industries without starting from scratch.
In the years to come, we may witness companies known for their warehouse robotics moving into the automotive realm, or established autonomous car manufacturers launching specialised AMR solutions for facilities of all kinds.
As these technologies continue to meet, engineers, investors, and enthusiasts in both sectors will have a front-row seat to one of the most exciting periods in the history of robotics and automation.
Legal Disclaimer:
MENAFN provides the information “as is” without warranty of any kind. We do not accept any responsibility or liability for the accuracy, content, images, videos, licenses, completeness, legality, or reliability of the information contained in this article. If you have any complaints or copyright issues related to this article, kindly contact the provider above.
Comments
No comment